초록
치과용 세라믹의 파절실험 후 파절이 발생한 원인을 분석하면 세라믹의 임상적용 가능성을 높일 수 있다. 파절원인을 파악하기 위한 파단면분석은 주사전자현미경 등 영상기술의 발달로 점차 널리 적용되고 있는데 이를 정확히 해석하기 위해서는 실험조건 설정이 중요하다. 파절시편이 오염되지 않도록 보관하고 세척하며, 관찰을 위해 금속 전처리가 필요하다. 파절은 양상에 따라 주로 금속에서 관찰되는 보조개모양 파절, 열개, 분리파손 및 세라믹에서 관찰되는 피로파절과 조가비 모양 파절이 있다. 세라믹의 주된 파절원인인 피로파절을 실험실에서 재현하기 위해 느린 균열성장을 관찰할 수 있는 동적 하중이 필수적이며 하중조건과 하중횟수 등을 적절히 설정해야 한다. 세라믹의 파단면에서 나타나는 대표적인 특징은 해클이며 다양한 해클의 형태를 잘 관찰하여 세라믹 파절의 원인과 과정을 분석할 수 있도록 하는 것이 필요하다. 파단면분석은 치과용 세라믹의 파절을 심층적으로 파악할 수 있는 유용한 방법이므로 정확한 실험과정을 따르고 결과 해석에 유의해야 한다.
Abstract
The clinical applicability of ceramics can be increased by analyzing the causes of fractures after fracture testing of dental ceramics. Fractography to analyze the cause of fracture of dental ceramics is being widely applied with the development of imaging technologies such as scanning electron microscopy. Setting the experimental conditions is important for accurate interpretation. The fractured specimens should be stored and cleaned to avoid contamination, and metal pretreatment is required for better observation. Depending on the type of fracture, there are dimple rupture, cleavage, and decohesive rupture mainly observed in metals, and fatigue fractures and conchoidal fractures observed in ceramics. In order to reproduce fatigue fracture in the laboratory, which is the main cause of fracture of ceramics, a dynamic loading for observing slow crack growth is essential, and the load conditions and number of loads must be appropriately set. A typical characteristic of a fracture surface of ceramic is a hackle, and the causes of fracture vary depending on the shape of hackle. Fractography is a useful method for in-depth understanding of fractures of dental ceramics, so it is necessary to follow the exact experimental procedure and interpret the results with caution.
적절한 심미성과 우수한 강도를 가진 세라믹은 치과용으로 널리 사용되고 있으나 내재된 취성(brittleness)으로 인해 교합력이 잘 조절되지 않거나 하부구조의 디자인이 잘못된 경우 보철물의 파절 및 부분파절이 발생할 수 있다(Fig. 1).1
파절이 발생한 원인은 다양하게 추정할 수 있으나 구조적 실패원인을 분석하기 위해서는 파절면에 대한 고배율의 사진으로 파절양상과 파절원인을 해석하는 파단면분석(fractography)이 사용되고 있다. 원래 파단면분석은 금속의 균열을 연구하는 금속조직학(metallography)에서 유래되었으며 광학현미경과 주사전자현미경(scanning electron microscope, SEM) 및 투과전자현미경(transmission electron microscope, TEM)의 기술발달이 더해지면서 세라믹에서도 미세기계적 원인으로 발생한 파절의 기시점과 성장 등 피로파절에 대한 과정을 설명하는 것이 가능해졌다.2
세라믹과 관련된 생체내(in vivo) 및 생체외(in vitro) 물성실험에서 파절된 단면을 분석하는 파단면분석법은 유용한 해석방법이지만 이를 이해하고 적절하게 적용하기 위해서는 주의가 필요하다. 파단면분석을 하기 위해 어떤 원리를 적용하여 실험시편을 제작하고 관찰하며 어떻게 해석해야 하는지 문헌을 고찰하고, 실제 실험을 진행하며 얻게 된 지식을 정리해 보고자 한다.
파절된 표면을 관찰하기 위해 광학현미경을 이용하여 배율을 조절하면 거시적, 미시적 형태를 파악할 수 있다. 투과전자현미경(TEM)은 광학현미경의 한계인 제한된 심도와 확대율의 장애를 극복할 수 있으나 파절편의 복제품을 제작해야 하며 시편을 제작하는데 상당한 어려움이 있다.2 하지만 주사전자현미경(SEM)의 기술이 발달하면서 큰 피사체 심도와 광범위한 배율을 적용할 수 있고 비파괴적으로 시편을 제작할 수 있으며 3차원적인 형태를 관찰할 수 있어 SEM이 파단면분석에 일반적으로 사용되고 있다.
SEM은 전자선이 전도성 시편을 가로질러 이동하면서 구조와 조성에 관한 다양한 정보신호를 방출하는 현상을 이용하는데 초기에 사용하던 광자 대신 전자선을 이용하면서 해상도를 향상시킬 수 있게 되었다.3 전자선이 시간-신호 상태로 조사되기 때문에 넓은 시야를 확보할 수 있고 상을 3차원적으로 관찰할 수 있어 표면결함이나 파단면 검사에 이상적인 기구이다.
SEM으로 작업할 때 결과에 영향을 미치는 요인을 잘 파악해야 활용도를 높일 수 있다. 시편은 3차원적으로 조절하면서 위치시킬 수 있는데, z-축은 시편의 높이(작업거리)를 조절하기 때문에 관찰범위(depth of field)와 배율을 결정하는데 중요하다. 작업거리가 증가하면 관찰범위가 넓어지지만 배율이 낮아야 하므로 적절한 영상을 얻으려면 시편표면을 전자탐지기 수준이나 바로 하방에 위치시키는 것이 좋다. 명확한 영상을 얻으려면 시편의 경사를 조절하게 되는데 이상적인 각도는 시편의 형태에 따라 달라지며 더 부드러운 시편은 더 큰 각도로 관찰해야 한다. SEM으로 관찰하면서 모니터에서 대조도와 명도를 확인하고 조절해야 한다. 낮은 배율에서 높은 배율로 가면서 점진적으로 관찰하고 기록하는 것이 필요하다(Fig. 2).
SEM 관찰을 위해 시편은 전도성이어야 하며, 깨끗하고, 현미경 관찰범위에 포함시킬 수 있을 만큼 충분히 작아야 하며 표본이 과도하게 클 경우에는 복제품을 제작해야 한다. 금속은 직접 관찰이 가능하므로 시편을 세척 후 전도성 테이프를 이용하여 고정한 후 관찰하지만, 비전도성 시편은 매우 낮은 가속전압(5 keV)으로 관찰하지 않으면 적절히 관찰할 수가 없기에 복제품을 만들거나 전도성을 가진 물질을 코팅하여 관찰한다.4 표본을 코팅하면 더 높은 전압(15 - 20 keV)을 사용할 수 있어 영상의 질을 향상시킬 수 있다. 금속성 코팅(gold, chromium)이 선호되는데 열증발법(thermal evaporation) 또는 스퍼터방법(sputter coating)을 주로 이용한다(Fig. 3).5 하지만, 표면을 코팅한 시편은 이후 실험과정에서는 원 상태로 복구하기가 매우 어려우므로 실험의 마지막 단계에서 코팅을 하는 것이 좋다.
구강 내에서 파절된 세라믹 수복물의 경우 제거하기 어려운 경우가 많아 Scherrer 등6은 시편을 복제하여 관찰하는 방법을 제시하였다. 이 방법에 따르면 파절면을 알코올로 세척하고 건조시킨 후 실리콘 인상재를 파절면에서부터 시작해서 교합면 전체에 분사하여 인상을 채득하고 이후 에폭시레진을 부은 후 금으로 코팅을 함으로써 파절의 시작과 진행방향을 분석할 수 있다고 하였다(Fig. 4). 실제 이 방법을 적용하여 실험할 때는 에폭시레진의 혼합에 상당히 유의해야 한다. 임상에서 사용하는 PMMA (polymethyl methacrylate)와는 달리 에폭시레진은 수지와 경화제 모두 점성을 띄어 충분히 혼합하지 않을 경우 최종경화가 발생하지 않는다.7 따라서 오랜 시간 충분히 혼합하여야 하고, 혼합 중에 기포가 유입될 수 있기 때문에 스파츌라를 러버볼에 대고 누르면서 혼합해야 한다. 충분히 혼합 후에 실리콘에 적용할 때에도 큰 기포가 발생할 수 있으므로, 중요하지 않은 부위부터 흘러 들어가도록 조심스럽게 적용해야 한다.
파절 시편의 준비와 보관도 중요한데, 파절면은 손상되기 쉬우며 미세구조의 특징을 파괴할 수 있는 기계적, 환경적 영향을 받기 쉬우므로 분석의 모든 과정에서 주의 깊게 다루어야 한다. 특히 시편을 준비하는 과정에서 손상되면 파절면 해석을 방해할 수 있다. 이러한 손상은 파절 후에 처해진 환경에 기인하는 화학적 손상과 하중의 결과로 발생하는 기계적 손상으로 나눌 수 있다.8 화학적 손상은 주로 비귀금속의 부식으로 발생하는데 파절된 단면이 수분과 염분이 있는 환경에 있으면 철과 비귀금속을 산화시키기 때문이다. 하지만 이러한 산화는 너무 심하게 손상된 것만 아니라면 어느 정도의 처리에 의해 관찰이 가능한 정도까지 회복할 수 있다. 반면, 파절 당시 하중을 받고 있는 상태에서 파절면이 서로 접촉하게 되어 손상되거나, 파절면을 맞추어 보고 날카로운 기구로 긁는 등 취급 또는 이동 중에 발생하는 기계적 손상은 원래의 파절형태로 되돌릴 수 없기에 이러한 행위를 하지 않도록 특별히 주의해야 한다. 모든 파절면을 먼저 확인하여 균열기시부의 위치를 대략적으로 지정하는 것이 미세한 분석을 위해 어떤 부위를 구체적으로 관찰할지 전략을 결정하는데 유리하다. 파절 즉시 파절면을 평가할 수 없을 때는 환경적, 기계적 손상을 받지 않도록 즉시 보존해야 하는데, 가장 좋은 보존법은 압축공기로 건조시킨 후 진공이나 건조제가 들어있는 용기에 보관하는 것이지만 이는 실용적이지는 않으므로 산화와 부식을 방지할 수 있는 표면코팅이 필요하다.9 코팅 시 파절의 원인을 밝힐 수 있는 표면의 파편이 사라질 수도 있으므로 다시 표면의 파편을 회복시킬 수 있도록 화학적으로 반응하지 않으며, 환경으로 인한 손상을 막을 수 있고 파절면을 손상시키지 않은 상태로 완전히 제거할 수 있는 코팅이 필요하다. 이 때 투명 라커(clear acrylic lacquer) 또는 플라스틱 코팅(plastic coating)을 파절면에 분사하고 필요에 따라 유기용매로 제거하기도 하는데 거친 면의 경우 완전한 코팅이나 제거가 어려워 가급적 이런 방법을 피하는 것이 좋다. 셀룰로즈 테이프(cellulose acetate replicating tape)는 다양한 두께로 적용할 수 있으나 거친 표면의 경우 다른 방법과 마찬가지로 완전히 제거하기 어렵다. 석유화합물(petroleum base compounds)은 적용이 쉽고 유기용매를 넣고 초음파세척기에 넣으며 쉽게 제거되어 추후 제거가 필요하다면 이 방법을 이용하는 것이 좋다.
다양한 환경에 노출 시 파절된 표면에 먼지, 부식, 산화물 등이 부착되므로 파절면을 세척하는 것도 중요한데, 세척 전 저배율의 입체현미경으로 파절면의 사진을 남겨 놓고 세척 후 결과를 비교함으로써 세척과정에서 손상된 부분이 없는지 확인해야 한다. 가장 부드럽고 덜 공격적인 세척방법을 먼저 이용하고 잔유물이 남아 있다면 좀 더 강한 세척방법을 사용하는 것이 좋다. 가장 간단한 세척방법은 압축공기를 불거나 부드러운 붓으로 부착된 입자나 먼지를 제거하는 것이다. 복제코팅을 제거하거나 유기용매(xylene, naphtha, toluene, freon, ketones, alcohols)를 파절된 단면의 유분이나 잔사를 제거하기 위해 사용할 수 있다.9 이 때 유기용매로 충분한 시간 동안 세척하고 파절면에는 깨끗한 유기용매만 닿도록 해야 한다. 가장 편하게 사용할 수 있으며 효과적인 방법은 앞서 언급했던 유기용매를 초음파세척기와 함께 사용하는 것이다. 그렇지만 파절면 해석에 주요한 입자이거나 파절면과 관련된 부분에 이물질이 위치되어 있을 때에는 제거 전에 화학적인 조성을 먼저 조사하는 것이 추천된다. 철이나 알루미늄 재료와 같은 경우는 세척제와 물을 함께 사용하여 초음파세척기를 이용하면 잔사제거에 효과적이다. 표면이 화학적으로 오염되지 않은 철의 경우는 음극세척(cathodic cleaning)을 시행하기도 한다.7 약산 또는 약염기 용액을 이용한 표면의 화학적 세척은 파절면에 대한 화학적 손상의 가능성이 있어 가급적 최후에 사용한다. 금속의 경우 다양한 용액(acetic acid, phosphoric acid, sodium hydroxide, ammonium citrate, ammonium oxalate solution 등)을 이용하여 세척한다.8,9
파절된 시편이 너무 크거나 수리가 필요할 때는 파절면 부분만의 분할이 필요하여 어쩔 수 없이 시편을 절단하게 되는데, 절단 전 분할하는 위치를 정확히 기록해 놓고 절단과정에서도 열에 의해 구조가 변형 또는 손상되지 않도록 충분한 거리를 두고 절단해야 한다. 냉각제에 의해 파절면이 부식되거나 해석에 중요한 부분이 씻겨 없어질 수 있으므로 건조한 상태에서 절단하는 것이 유리하지만 파절부와 충분한 거리를 유지할 수 없을 때는 열손상을 피하기 위해 냉각제가 필요하다. 이 때는 파절면 상부를 코팅하여 절단하고 과정이 끝나면 바로 용매로 세척하는 것이 좋다.
파절특징을 기록하는데 사진은 중요한 역할을 한다. 중요한 특징과 관계가 있는 부위에 대한 사진을 찍음으로써 확대를 시행할 배율과 파절특징에 대해 유추할 수 있기 때문에 직접 조명을 이용하여 다양한 각도에서 파절면의 특징을 평가한 후 적절한 배율을 정하여 파절면의 사진을 촬영한다. 이후 입체현미경을 이용하여 사진을 찍는데, 입체현미경은 광축 사이에 약 15도로 벌어진 2개의 광속에 의해 정립한 확대상을 만들고, 이것을 각각의 눈으로 봄으로써 입체감을 얻는 원리이다.2 입체현미경은 금속과 생물체에 모두 사용 가능하며 작업거리가 길기 때문에 시편을 보면서 작업을 할 수 있고 작업거리의 한계배율은 50배 정도이다. 가장 일반적으로 사진을 기록하는 방법은 SEM인데 파면을 손상시키지 않고 직접적으로 관찰할 수 있으며 깊은 초점심도와 폭넓은 배율변화가 가능하며 파면에 대한 3차원 영상촬영이 가능하여 많이 이용된다.
파절은 재료의 결정 사이로 또는 결정을 통해 진행되는데, 파절이 된 단면은 파절의 진행방향과는 상관없이 5가지의 양상으로 분류할 수 있으며 각각의 특징이 존재한다.10 대부분의 파단면 양상은 금속에 해당하는 것이며 이 중 피로파절에 의한 양상이 세라믹에서 나타난다.11
보조개 모양 파절(dimple rupture)은 재료의 파단면이 보조개처럼 파인 모양을 나타내는 연성파절의 대표적 형상으로 과하중이 실패의 원인일 때 발생한다.12 재료 내부에서 변형 불일치(strain discontinuity)가 발생한 부위에 응력이 집중되는데, 재료 내부의 긴장도가 점진적으로 높아지면 미세공간이 융합되고 커져 결과적으로 연속적인 파절면을 형성하게 된다. 이러한 형태의 파절은 오목한 그릇과 같은 형태로 나타난다(Fig. 5). 파절면에서 오목한 면(dimple)의 크기는 융합된 미세공간의 수와 분포에 의해 결정되며 융합부의 갯수가 적고 넓은 공간을 차지하면 파절면은 크고 오목한 표면을 형성하게 된다.12,13 또 재료 내부의 응력상태와 재료의 미세구조 및 가소성에 따라 다양한 형태를 보이게 된다. 즉, 한 방향으로 인장응력이 가해지는지, 양쪽에서 인장응력이 가해지는 상황인지(tear), 또는 전단응력이 가해지는지에 따라 오목한 면의 형태가 달라진다.12
열개(cleavage) 파단면은 다결정구조의 금속에서 발생하며 경계가 뚜렷하고 편평하며 반짝이고 반사되는 표면을 나타낸다.14 이는 결정평면을 따라 진행하는 낮은 에너지의 파절로 다수의 평행한 열개에서 시작되어 파절이 진행함에 따라 서로 합쳐지는 과정을 거치므로 작은 시냇물이 모여 강을 이루는 형태(river pattern)를 이루므로 열개의 형태를 보면 파절의 진행방향을 알 수 있다(Fig. 6).
분리파손(decohesive rupture)이란 입자경계에 있는 공동(void)이나 와동(cavity) 등에 응력이 가해지면 입자경계를 따라 균열이 성장하는 양상을 말한다(Fig. 7). 소성 변형이나 앞서 언급했던 3가지 형태의 파절과는 연관이 없으며 재료의 환경 또는 이물질과 같은 독특한 미세구조에 의해 발생한다.15 이러한 분리파손은 하나의 독립된 파절과정이 아니며 원자결합의 약화, 표면에너지의 약화, 분자가스의 압력, 보호필름의 파괴 등 여러 다른 요인에 의해 시작되고 금속에서 나타나는 독특한 파절양상으로 균열과 공동이 혼합되어 발생한다고 한다.15
재료에 주기적, 반복적인 하중이 가해지면 단계적으로 피로파절(fatigue)이 발생한다. 특히 낮은 강도의 응력이 장기간 가해질 때 발생한다고 알려져 있다.16 피로파절의 단계는 파절의 시작, 균열의 증식, 완전파절로 이루어진다(Fig. 8). 1단계인 파절의 시작단계는 재료의 피로수명 중 90% 정도의 시간에 해당한다고 한다.17 2단계인 균열의 증식에서는 전체 파절길이만큼 균열이 진행되는데 결정입자를 관통해서 균열이 진행된다. 이는 교대로 발생되는 응력의 크기에 의해 영향을 받는데, 그 증거는 균열정지표시(crack-arrest mark (fatigue striation으로 알려짐))로 알 수 있다.18 정상적인 상태에서 각 줄무늬는 한 하중 주기의 결과이고 줄무늬가 형성된 부분의 전방에 피로균열이 위치한다. 그렇지만 적용되는 하중이 갑자기 감소할 경우 균열 증식은 멈추게 되고 파절줄무늬(striation)가 생기지 않는다.17 이후 특정한 수의 작은 응력이 다시 반복적으로 적용되면 균열은 다시 증식하게 된다.19 균열이 재료가 감내할 수 있는 마지막 단계까지 도달하면 완전파절이 발생한다.
조가비 모양 파절(conchoidal fracture)이란 취성을 가진 재료에서 발생하는 파절로, 잘 정리된 분리평면을 따르지 않고 홍합껍질에서 보듯 잔금이 번져 나가는 단면이 일정하지 않고 우연한 형태의 파절을 말한다.20 재료의 고유특성에 따라 2 - 4개의 파편으로 나뉘는 낮은 강도, 10개 정도의 파편으로 나뉘는 중강도, 무수히 많은 파편으로 나뉘는 고강도의 파절로 나눌 수 있는데 치과용 세라믹은 대부분 한계응력에 비해 낮은 강도의 파절을 보이며 시작점에서 가지를 뻗는 양상이나 2차적인 파절이 거의 나타나지 않는다(Fig. 9).21
세라믹의 파절은 시기에 따라 진행되는 양상이 달라진다. 다양한 이유로 하중이 가해지는 지점에서 파절이 발생하는 임계점을 넘는 한계응력이 발생하는 부위가 균열의 기시점이 된다. 이후 방사형으로 균열이 진행되다가 국소적인 인장응력이 발생하면서 한 부위가 떨어져 나가는 것이다.
세라믹은 임계치보다 낮은 응력에서 파절이 발생하는 경우가 많은데 이는 표면의 결점이 서서히 커지기 때문이다.17 특히 수분이 있는 환경에서 세라믹 표면에 존재하는 균열은 여러가지 파괴작용을 유발할 수 있다. 구강내 환경은 타액, 저작력, 온도, pH라는 측면에서 세라믹 수복물에는 상당히 불리한 조건을 제공할 수밖에 없어 특히 균열에 민감하므로, 세라믹 재료는 높은 파절강도와 함께 균열저항성을 가져야 한다. 균열민감도(stress corrosion susceptibility coefficient (n))는 다양한 방법으로 측정할 수 있는데 동적인 실험을 통해 시간과 균열크기의 상관관계를 도출하는 방법을 사용할 수 있다.22 세라믹의 n은 미세구조의 차이, 결정입자의 구조, 부피율, 기질의 분포 등이 미세균열에 영향을 미치고 물리적 성질을 저하시킨다. Gonzaga 등23은 세라믹의 물성치인 파괴인성 및 임계파절 하중과 n간의 관계를 비교하였는데, 장석계 도재에 비해 리튬디실리케이트(lithium disilicate, LS2)나 유리질침투 세라믹이 높은 파괴인성을 가지고 시간이 지났을 때 균열이 커지는 정도도 1/3 정도로 작아 n도 높다고 하였다. 이는 결정입자 구조의 비율이 높은 LS2에서 미세구조의 물리적 특성이 파괴인성에 영향을 준 것으로 추정된다. 같은 LS2라도 결정입자의 구조와 길이에 따라 물성이 달라지기도 하는데 Lee 등24은 결정이 침상인 형태에 비해 구형일 때 결정입자의 밀도가 높아 경도가 더 높아진다고 하였다(Fig. 10).
결정의 크기나 구조에 따라 물성이 달라지는 현상은 지르코니아에서도 관찰되는데 Bravo-Leon 등25은 1 µm 이상의 결정입자 크기를 갖는 지르코니아에서 자발적인 상변이가 발생하여 저온열화현상에 취약해지는 현상이 나타난다고 하였다. 또한 결정입자의 크기가 0.9 µm에서 1.4 µm까지일때는 지르코니아의 파절강도가 증가하였으나 1.4 µm 이후부터 1.8 µm까지는 지르코니아의 파절강도가 점점 감소한다는 연구결과도 있다.25
세라믹은 정적인 실험을 통해 파괴되는 순간의 강도를 산출하면 매우 높은 파절강도를 가지지만 임상에서는 기계, 화학, 생물학적인 다양한 기여요인들이 관여하면서 표면에 발생한 결함(flaw)으로 인해 훨씬 낮은 응력에서 실패가 발생한다. 이러한 결함이나 균열은 기능 중에 아주 느린 속도로 성장하다가 어떤 임계값에 도달했을 때 급작스러운 속도로 진행되어 파괴적인 결과를 보이는 피로파절의 양상을 띠는 것이다.26,27 모든 세라믹은 균열이 진행되기 전에는 하중에 대해 견딜 수 있으므로, 기공이나 흠에 의한 느린 균열성장(slow crack growth, SCG)이 언제 결정적인 파괴지점에 도달하는지를 예측해야 한다. 이런 SCG 기전을 이해하면 표면연마가 왜 세라믹의 물성향상에 기여하는지 또, 왜 동적인 하중이 물성저하에 기여하는지 추론할 수 있다. 파절강도와 파절가능성을 분석하여 세라믹의 신뢰도를 분석하는 Weibull이 대표적인 SCG를 분석하는 방법이며 파절에 영향을 주는 임계값(threshold stress intensity factor, KI0)을 분석하는 방법도 있다. Marx 등28은 Vickers 압흔시험을 진행하고 균열이 성장한 직경을 측정하여 파절속도를 추정하는 방법으로 인장력이 재료에 균열을 유발하지 않는 한계인 임계값을 구하였다. 이 연구에 따르면 리튬디실리케이트에 비해 높은 파괴인성을 가지는 지르코니아도 임계값은 비슷하여 사람의 교합력 범위와 유사한 범위에서 파절이 시작된다고 하였다. 임계값은 동적하중의 결과인 파괴인성보다 더 본질적인 값으로 해석될 수 있으며, 파괴인성이 다른 재료인데 임계값이 유사하다는 것은 두 재료의 SCG에 동일한 시작점이 있음을 시사한다.
Quinn29은 타액의 수분에 의해 Si-O-Si 결합이 붕괴되어 Si-OH로 약화된 상태에서 저작력이 지속적으로 가해짐에 따라 SCG가 발생한다고 하였으며 Cesar 등30은 세라믹 실험에서 SCG를 분석할 수 있는 동적하중이 필수적인 실험조건이라고 하였다. 동적인 하중은 초기에는 세라믹의 강화기전에 일정 정도 기여하기도 하지만 하중의 조건과 하중을 받는 형태에 따라 물성저하를 유발하기도 하므로 임상상황에 가장 가까운 하중방법이다. 동적인 하중의 가장 큰 장점은 세라믹에서만 나타나는 SCG를 잘 예측할 수 있다는 것이다. 동적 하중은 시간이 많이 필요하다는 단점이 있으므로 적절하게 하중을 설계해서 원하는 결과를 도출해야 한다. 시간의 측면에서 계단식 응력을 사용하기도 하나, 결과에 대한 해석의 한계가 있을 수 있으므로 대부분 최소응력과 최대응력의 반복으로 하중을 가하며 105 - 106의 주기에서 주로 파절이 발생하므로 최소 하중횟수를 설정할 때 고려해야 한다.17,30 하지만 이런 실험조건을 사용하더라도 파절에 대한 정확한 정보를 얻으려면 어떤 위치에서 균열이 시작하고 성장했는지 확인하기 위해 추가적으로 SEM을 이용하여 파단면을 분석하는 것이 필요하다.
유리와 세라믹같이 취성이 있는 물질에서 파절은 갑작스럽게 파괴적으로 일어나는 불안정한 과정이다. 파단면 분석 시 파손된 부분의 응력이 클수록 저장된 에너지가 많고 드러나는 특징이 많아 해석이 쉬운 반면, 저장된 에너지가 낮으면 뚜렷한 특징이 없는 두 조각으로 나뉘어 해석하기가 어려울 수 있다. 또한 부드러운 입자에 비해 다공성이거나 거친 입자를 가진 물질일수록 파절의 특징들을 잘 파악할 수 있다.31 파단면은 파절의 원인을 파악하는데 많은 정보를 내포하고 있으므로 파단면을 적절히 분석하기 위해서는 용어를 알고 그 의미를 알아야 한다(Fig. 11).
취성 파괴가 시작되는 근원을 파절의 기시점(origin, O)이라고 하는데 물질내 결함이 있어 가장 불리한 조건의 인장력이 발생하는 지점이다.32 기시점을 기준으로 파절이 방사형으로 퍼져 나가므로 기시점을 분석하면 재료의 결점과 응력의 크기 및 집중을 알 수 있다. 때로 복합적인 파절로 인해 기시점을 알 수 없을 때는 응력의 상태, 균열의 속도, 균열의 진행방향을 통해 기시점을 역추적하여 알아낼 수도 있다.
기시점을 감싸고 있는 원형의 매끄러운 부분을 평활 거울영역(mirror, Mir)이라고 하는데 기시점에 비해 잠재된 에너지가 작아 균열의 진행속도가 느린 상태이므로 면이 나누어지거나 편향되지 않기 때문에 편평하고 보다 매끄러운 모습을 보인다.11 기시점을 항상 파악할 수 있는 것은 아니지만 Mir은 잘 관찰할 수 있는데 비교적 쉽게 구분할 수 있는 명백한 특징을 가지기 때문이다. 특히 Mir의 반경은 잔류응력과 비례하기 때문에 집중된 인장력이 강할 때 Mir이 잘 관찰된다. 하지만 파절의 기시점이 여러 곳이거나 재료 자체의 흠이 많으면 Mir을 관찰하기 어렵고 임상에서 나타나는 세라믹의 파절은 SCG로 인해 흠이 크고 많기 때문에 Mir을 거의 관찰하기 어렵다. 하지만 대부분 실험실에서 유도한 파절상황에서는 Mir을 관찰할 수 있다. 만약 정적인 하중시험에서 Mir이 관찰되지 않는다면 설계한 실험의 하중이 적절하지 않았다고 추측할 수 있다.33
Mir 바깥으로 안개처럼 퍼져 있는 부분이 안개영역(Mis) 영역인데 균열의 진행속도에 가속이 붙어 빨라지면서 최고속도에 도달하면 잠재된 에너지가 주변에 방산되어 외층보다는 덜 거친 부위를 형성하는 것이다. Mis는 따로 분류하기도 하지만 해클(hackle, 잔금)의 한 종류로 취급하기도 한다.
해클은 균열이 진행되는 방향을 나타내는 결정적인 표시로 균열이 있는 표면에 나타나는 선이다. 에너지가 두번째 균열을 형성할 만큼 충분한 경우에 형성되며 균열의 증식과 평행하게 주행하지만 동일한 평면이 아닌 부분이다. 원인과 나타나는 양상에 따라 여러가지로 나뉜다.34 이 중 웨이크 해클(wake hackle)은 균열방향의 앞쪽에서 나타나는 불규칙한 선으로, 균열이 진행되면서 다공성 세라믹 재료 내의 공기나 흠이 있는 부위를 지나 다시 합쳐지면서 꼬리형태로 다시 평행하게 진행되는 것이다. 비교적 저배율에서 관찰되는데 식별이 가장 쉬우며 파절의 기시부를 추측하는데 가장 유리한 표식이다.35
벨로시티 해클(velocity hackle)은 바깥쪽으로 방사되는 해클의 형태로 앞면의 높이가 다르게 나타나거나 큰 단도와 같은 모양을 지닌 부위로 이 부위에서는 균열의 속도가 일정하게 진행되며 높은 응력이 발생했음을 말해 주는 것이다.36 이는 균열이 시작되고 종단속도에 도달하기 전까지 Mis 외곽에 나타난 균열방향을 표시하는 해클로, 균열방향과 평행하게 정렬된 방향으로 나타난다. 세라믹의 특징적인 미세구조로 인하여 Mis의 정확한 경계를 식별하기가 매우 어려워 벨로시티 해클의 기시부도 관찰하기 힘든 경우가 많다. 하지만 관찰할 수 있다면 파절의 근원지인 Mir 부위와 Mis 이후 균열의 진행방향을 나타내는 주요한 지표가 된다.
트위스트 해클은 주된 인장력에 의해 균열이 진행되는 방향에서 측방으로의 회전이나 비틀림과 같은 국소적인 전단응력이 가해지거나 구조적 비동질성이 있을 때, 원래의 균열면에서 틀면서 다른 평면에 압축응력이 발생되어 나타나는 표식이다.23 균열의 진행방향과 평행하기 때문에 기시점을 추측할 때 도움이 된다. 모서리나 불균질한 형태가 있을 때 나타나기도 한다. 이러한 트위스트 해클은 치과용 세라믹에서 특히 중요한데 다공성인 LS2 같은 경우는 응력조건이 자주 변할 때 발생하며 지르코니아에서는 내부의 입자크기 차이에 의해 발생할 수 있다. 균열의 진행평면에서 국소적으로 퍼진 부분(segment)들이 발생하고 이런 부분들이 이어지면서 트위스트 해클이 발생하는 것이다.
또 다른 대표적인 해클은 인장응력에 의해 균열이 진행하는 방향에 대해 수직으로 발생하는 것인데 대표적으로는 균열의 뒷면에 있는 Wallner선과 균열의 앞면에 생기는 정지선(arrest line)이 있다. 이 중 Wallner선은 균열선이 팽창하여 나타나는 탄성파로, 팽창하는 탄성파에 의해 균열선이 어떻게 추월되었는지 보여 준다.34 Wallner선은 연못 표면의 파도처럼 순간적으로 일어나는 파문이 흔적으로 남게 되므로 부드러운 흔적으로 남아서 SEM으로 관찰하기는 힘들고 얇은 그림자 띠처럼 보이며 조명을 조정하면 보이는 부분이 약간 이동하는 경향이 있다.
정지선은 정지 해클이라고도 부르며 인장응력장의 변화로 인해 나타나는 날카로운 선이다. 균열이 성장해 가다가 멈출 때 형성되는 반원형의 선이다. Wallner선이 균열보다 더디게 오는 탄성파에 의한 흔적이라고 하면, 정지선은 균열의 전면에서 응력구성의 변화로 인해 나타나는 해클이다.6,34 균열은 국소적으로 최대 인장응력 방향에 대하여 수직으로 진행되지만 추가적으로 다른 장력이 개입하면 균열평면을 변화시킬 수도 있다. 이렇게 변화된 평면이 남기는 흔적은 Wallner선과 해클을 통해 분석할 수도 있다.
압축컬(compression curl 또는 cantilever curl)은 물체의 파절이 발생하기 전 날(lip) 모양의 형태로 형성되는 파단면의 특징으로 굽힘력(bending moment)을 받는 부위, 주로 균열의 바깥부분에서 나타난다.37 즉, 파절이 발생한 물체의 파단면 분석을 통해 압축컬이 나타난 부위는 굽힘력이 작용한 부위임을 증명하는 것이다. 이를 이용하여 굽힘강도 실험을 할 때는 하중을 가한 부위에서 압축컬이 나타나는지를 확인하여 의도한 곳에 하중이 가해졌는지 확인할 수도 있다. 임상상황에서는 세라믹 수복물 내면에서 발생한 인장력에 의해 주로 파절이 일어나므로, 파절이 시작된 부분과 반대되는 부위 즉 교합면 부위에서 드물게 나타난다.
이상과 같이 파단면의 형태는 다양하며 이를 잘 분석함으로써 파절의 시작과 진행을 알 수 있고 더 추가적인 분석을 통해 파절의 원인도 파악할 수 있으므로 파절의 기시점과 각각의 해클을 해석할 수 있어야 한다.
세라믹의 파절기전을 규명하기 위해 파단면분석을 할 때는 주사전자현미경의 작업거리와 관찰범위를 잘 설정해야 하며 골드코팅으로 더 정확한 분석이 가능하다. 파절시편은 기계적, 화학적 손상이 가해지지 않도록 보관해야 하며 파절면에 위해가 가해지지 않는 약한 세척부터 점진적으로 사용한다. 파절양상은 연성파절인 보조개모양 파절, 경계가 뚜렷한 열개, 이물질과 같은 미세구조가 관여하는 분리파손 등을 금속에서 관찰할 수 있다. 세라믹은 균열과 연관된 피로파절이 주된 파절양상이고 취성을 가지므로 때로는 조가비 모양 파절이 발생할 수도 있다. 이러한 파절을 관찰하기 위해서는 세라믹의 느린 균열성장을 관찰하고 파절속도를 추정할 수 있도록 하중조건과 하중횟수 등을 적절히 설정하여 동적 하중을 부여해야 한다. 세라믹의 파단면 분석 시 특징적인 형태를 해클이라 하는데, 파절원인에 따라 나타나는 형태가 다양하므로 해클 형태를 잘 파악하여 파절의 원인을 추정할 수 있어야 한다.
References
1. Lawson NC, Burgess JO. 2014; Dental ceramics: a current review. Compend Contin Educ Dent. 35:161–6. PMID: 24773195.
2. Lynch SP, Moutsos S. 2006; A brief history of fractography. J Fail Anal Prev. 6:54–69. DOI: 10.1361/154770206X156231.


3. Kemmenoe BH, Bullock GR. 1983; Structure analysis of sputter coated and ion beam sputter coated films: a comparative study. J Microsc. 132:153–63. DOI: 10.1111/j.1365-2818.1983.tb04267.x. PMID: 6358510.
4. Mills K, Davis JR, Destefani JD, Dieterich DA. 1998. ASM Handbook. Vol. 12. Fractography. Available from: https://docero.tips/doc/asm-handbookvolume-12-fractography-1998s-16d34vnnvl. updated 2022 Sep 1.
5. Hein LR, Campos KA, Caltabiano PC, Kostov KG. 2013; A brief discussion about image quality and SEM methods for quantitative fractography of polymer composites. Scanning. 35:196–204. DOI: 10.1002/sca.21048. PMID: 22915360.


6. Scherrer SS, Quinn JB, Quinn GD, Wiskott HW. 2007; Fractographic ceramic failure analysis using the replica technique. Dent Mater. 23:1397–404. DOI: 10.1016/j.dental.2006.12.002. PMID: 17270267. PMCID: PMC2077838.


7. Yamini S, Young R. 1979; Crack propagation in and fractography of epoxy resins. J Mater Sci. 14:1609–14. DOI: 10.1007/BF00569280.


8. Echlin P. 2011. Handbook of sample preparation for scanning electron microscopy and X-ray microanalysis. 1st ed. Springer Science & Business Media;New York: DOI: 10.1007/b100727_3.
9. Young R, Buxbaum A, Peterson B, Schampers R. 2008; In-situ sample preparation and modeling of SEMSTEM imaging. Microsc Microanal. 14:1000–1. DOI: 10.1017/S1431927608081713.


10. Scherrer SS, Quinn JB, Quinn GD, Kelly JR. 2006; Failure analysis of ceramic clinical cases using qualitative fractography. Int J Prosthodont. 19:185–92. PMID: 16602369.
11. Mecholsky JJ Jr. 1995; Fractography: Determining the sites of fracture initiation. Dent Mater. 11:113–6. DOI: 10.1016/0109-5641(95)80045-X. PMID: 8621031.


12. Sujata M, Jagannathan N, Raghavendra K, Manjunatha CM, Bhaumik SK. 2013; Fatigue fracture of a compressor disc of an aerogenine. J Fail Anal Preven. 13:437–44. DOI: 10.1007/s11668-013-9688-z.
13. Hasnaoui A, Van Swygenhoven H, Derlet PM. 2003; Dimples on nanocrystalline fracture surfaces as evidence for shear plane formation. Science. 300:1550–2. DOI: 10.1126/science.1084284. PMID: 12791986.


14. Liu P, Li Y, Geng H, Wang J. 2007; Microstructure characteristics in TIG welded joint of Mg/Al dissimilar materials. Mater Lett. 61:1288–91. DOI: 10.1016/j.matlet.2006.07.010.


15. De Saude J, Sun SD, Sharp P, Luzin V, Klein A, Wang C, Brandt M. 2016; Fatigue and fracture behavior of laser clad repair of AerMet® 100 ultra-high strength steel. Int J Fatig. 85:18–30. DOI: 10.1016/j.ijfatigue.2015.11.021.


16. Salazar Marocho SM, Studart AR, Bottino MA, Della Bona A. 2010; Mechanical strength and subcritical crack growth under wet cyclic loading of glass-infiltrated dental ceramics. Dent Mater. 26:483–90. DOI: 10.1016/j.dental.2010.01.007. PMID: 20303160.


17. Kelly JR, Cesar PF, Scherrer SS, Della Bona A, van Noort R, Tholey M, Vichi A, Lohbauer U. 2017; ADM guidance-ceramics: Fatigue principles and testing. Dent Mater. 33:1192–204. DOI: 10.1016/j.dental.2017.09.006. PMID: 29017761.


18. Taskonak B, Griggs JA, Mecholsky JJ Jr, Yan JH. 2008; Analysis of subcritical crack growth in dental ceramics using fracture mechanics and fractography. Dent Mater. 24:700–7. DOI: 10.1016/j.dental.2007.08.001. PMID: 17845817. PMCID: PMC2358925.


19. Kirsten A, Begand S, Oberbach T, Telle R, Fischer H. 2010; Subcritical crack growth behavior of dispersion oxide ceramics. J Biomed Mater Res B Appl Biomater. 95:202–6. DOI: 10.1002/jbm.b.31703. PMID: 20737435.


20. Song XF, Yin L, Peng JH, Lin B. 2013; Cutting characteristics of dental glass ceramics during in vitro dental abrasive adjusting using a high-speed electric handpiece. Ceram Int. 39:6237–49. DOI: 10.1016/j.ceramint.2013.01.045.


21. Song XF, Ma HR, He YP, Yin L. 2022; Soft machininginduced surface and edge chipping damage in precrystalized lithium silicate glass ceramics. J Mech Behav Biomed Mater. 131:105224. DOI: 10.1016/j.jmbbm.2022.105224. PMID: 35413493.


22. Teixeira EC, Piascik JR, Stoner BR, Thompson JY. 2007; Dynamic fatigue and strength characterization of three ceramic materials. J Mater Sci Mater Med. 18:1219–24. DOI: 10.1007/s10856-007-0131-4. PMID: 17277977.


23. Gonzaga CC, Cesar PF, Miranda WG Jr, Yosimura HN. 2011; Slow crack growth and reliability of dental ceramics. Dent Mater. 27:394–406. DOI: 10.1016/j.dental.2010.10.025. PMID: 21185074.


24. Lee YJ, Huh YH, Ko KH, Park CJ, Cho LR. 2022; Evaluation of various polishing systems for lithium disilicate glass-ceramics. Eur J Prosthodont Restor Dent. 30:188–99. DOI: 10.1922/EJPRD_2332Lee12. PMID: 34862863.
25. Bravo-León A, Jiménez-Melendo M, Domínguez-Rodríguez A. 1992; Mechanical and microstructural aspects of the high temperature plastic deformation of yttria-stabilized zirconia polycrystals. Acta Metal Mater. 40:2717–26. DOI: 10.1016/0956-7151(92)90342-C.


26. Eichle J, Rödel J, Eisele U, Hoffman M. 2007; Effect of grain size on mechanical properties of submicrometer 3Y-TZP: fracture strength and hydrothermal degradation. J Am Ceram Soc. 90:2830–6. DOI: 10.1111/j.1551-2916.2007.01643.x.


27. Smith TB, Kelly JR, Tesk JA. 1994; In vitro fracture behavior of ceramic and metal-ceramic restorations. J Prosthodont. 3:138–44. DOI: 10.1111/j.1532-849X.1994.tb00144.x. PMID: 7874255.


28. Marx R, Jungwirth F, Walter PO. 2004; Threshold intensity factors as lower boundaries for crack propagation in ceramics. Biomed Eng Online. 3:41. DOI: 10.1186/1475-925X-3-41. PMID: 15548323. PMCID: PMC539288.


29. Quinn GD. 2007. Fractography of ceramics and glasses. 3rd ed. National Institute of Standards and Technology;Washington: p. 233–5. DOI: 10.1111/j.1532-849x.1994.tb00144.x.
30. Cesar PF, Della Bona A, Scherrer SS, Tholey M, van Noort R, Vichi A, Kelly R, Lohbauer U. 2017; ADM guidance-Ceramics: Fracture toughness testing and method selection. Dent Mater. 33:575–84. DOI: 10.1016/j.dental.2017.03.006. PMID: 28392020.


31. Scherrer SS, Cattani-Lorente M, Vittecoq E, de Mestral F, Griggs JA, Wiskott HW. 2011; Fatigue behavior in water of Y-TZP zirconia ceramics after abrasion with 30 μm silica-coated alumina particles. Dent Mater. 27:e28–42. DOI: 10.1016/j.dental.2010.10.003. PMID: 21056462. PMCID: PMC3249662.
32. Quinn GD, Eichler J, Eisele U, Rodel J. 2004; Fracture mirrors in nanoscale 3Y TZP. J Am Ceram Soc. 87:513–6. DOI: 10.1111/j.1551-2916.2004.00513.x.
33. Preis V, Behr M, Hahnel S, Handel G, Rosentritt M. 2012; In vitro failure and fracture resistance of veneered and full-contour zirconia restorations. J Dent. 40:921–8. DOI: 10.1016/j.jdent.2012.07.010. PMID: 22835417.


34. Quinn GD. 2020. Fractography of ceramics and glasses. 3rd ed. National Institute of Standards and Technology;Washington: p. 108–256. DOI: 10.1016/j.jdent.2012.07.010.
35. Quinn JB, Quinn GD, Kelly JR, Scherrer SS. 2005; Fractographic analyses of three ceramic whole crown restoration failures. Dent Mater. 21:920–9. DOI: 10.1016/j.dental.2005.01.006. PMID: 15882898.


36. Scherrer SS, Quinn JB, Quinn GD, Kelly JR. 2006; Failure analysis of ceramic clinical cases using qualitative fractography. Int J Prosthodont. 19:185–92. PMID: 16602369.
37. Scherrer SS, Lohbauer U, Della Bona A, Vichi A, Tholey MJ, Kelly JR, van Noort R, Cesar PF. 2017; ADM guidance-Ceramics: Guidance to the use of fractography in failure analysis of brittle materials. Dent Mater. 33:599–620. DOI: 10.1016/j.dental.2017.03.004. PMID: 28400062.


Fig. 1
Partial fracture (chipping) of ceramics in metal ceramic prosthesis. (A) Partial fracture of more than half of the crown in the maxillary left second molar (red arrow), (B) Partial fracture at the maxillary right canine incisal edge (red arrow).
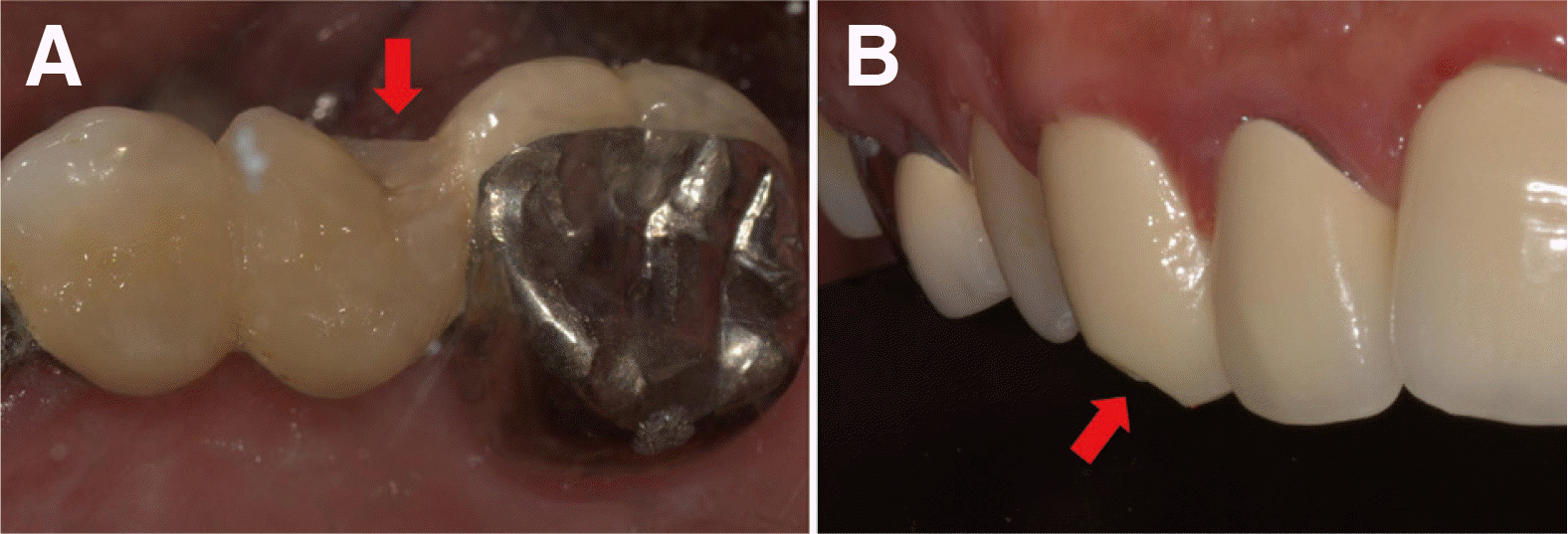
Fig. 2
Images observed while magnifying the same fracture surface (dotted line) from low to high magnification. (A) 30x magnification, (B) 50x magnification, (C) 100x magnification. The overall aspect of the fracture can be observed in the low magnification image, and the higher the magnification, the more detailed the fracture surface can be observed. The suspected origin and causes of the fracture can be estimated in higher magnification images.
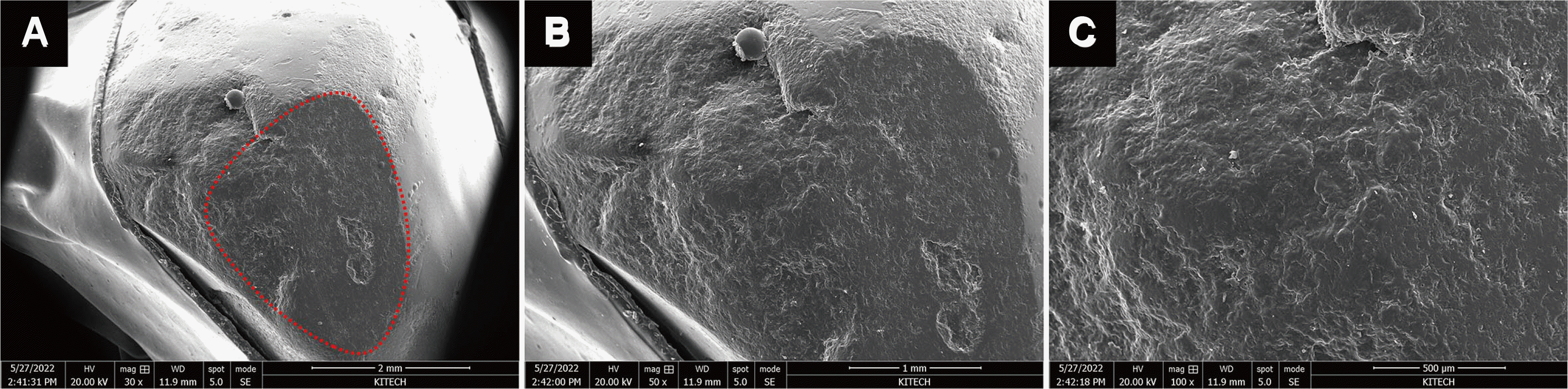
Fig. 3
Comparison of images before and after sputter coating. (A) SEM image of zirconia before gold coating, (B) SEM image of zirconia after gold coating. The microstructure of zirconia can be better observed in gold coating surface.
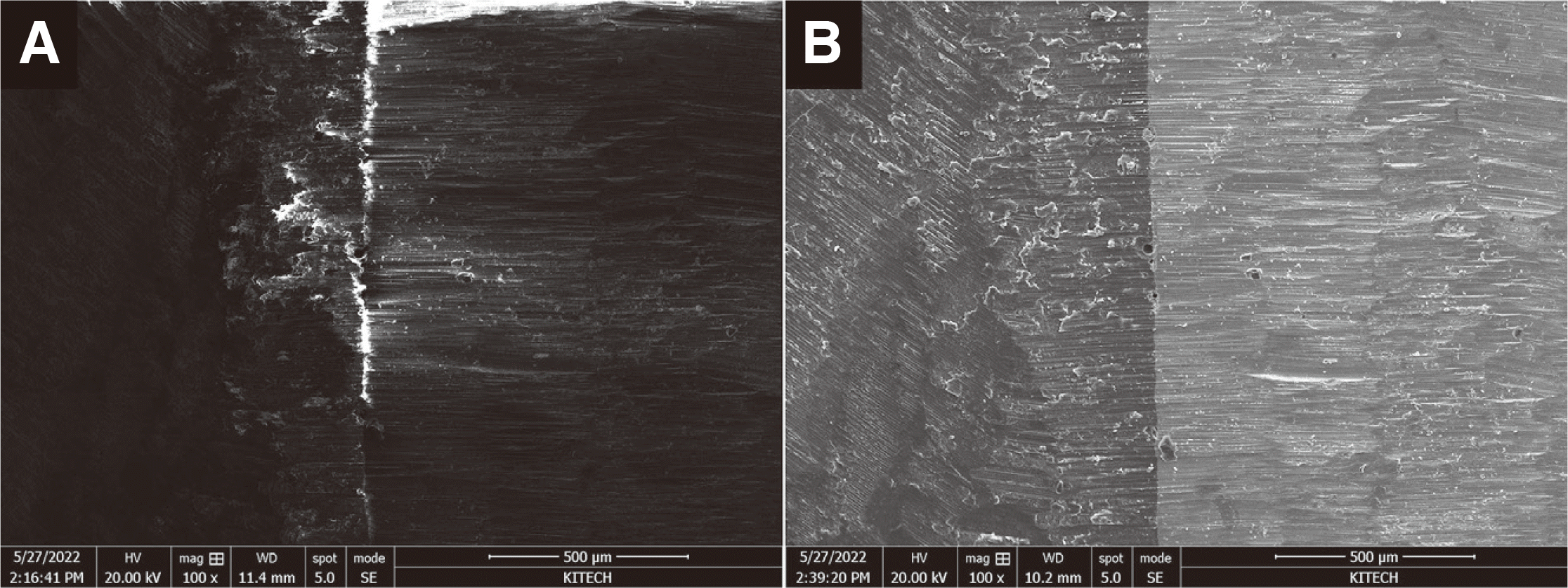
Fig. 4
(A) Partial fracture (chipping: red arrow) of ceramic restoration in maxillary right central incisor, (B) Replica technique using polyvinylsiloxane silicone impression material, (C) Silicone replica of fracture surface (red arrow), (D) Replica of fracture surface (red arrow) made with epoxy resin, (E) SEM image of epoxy resin replica after gold coating. Fracture surface characteristics (red arrow) can be observed well.
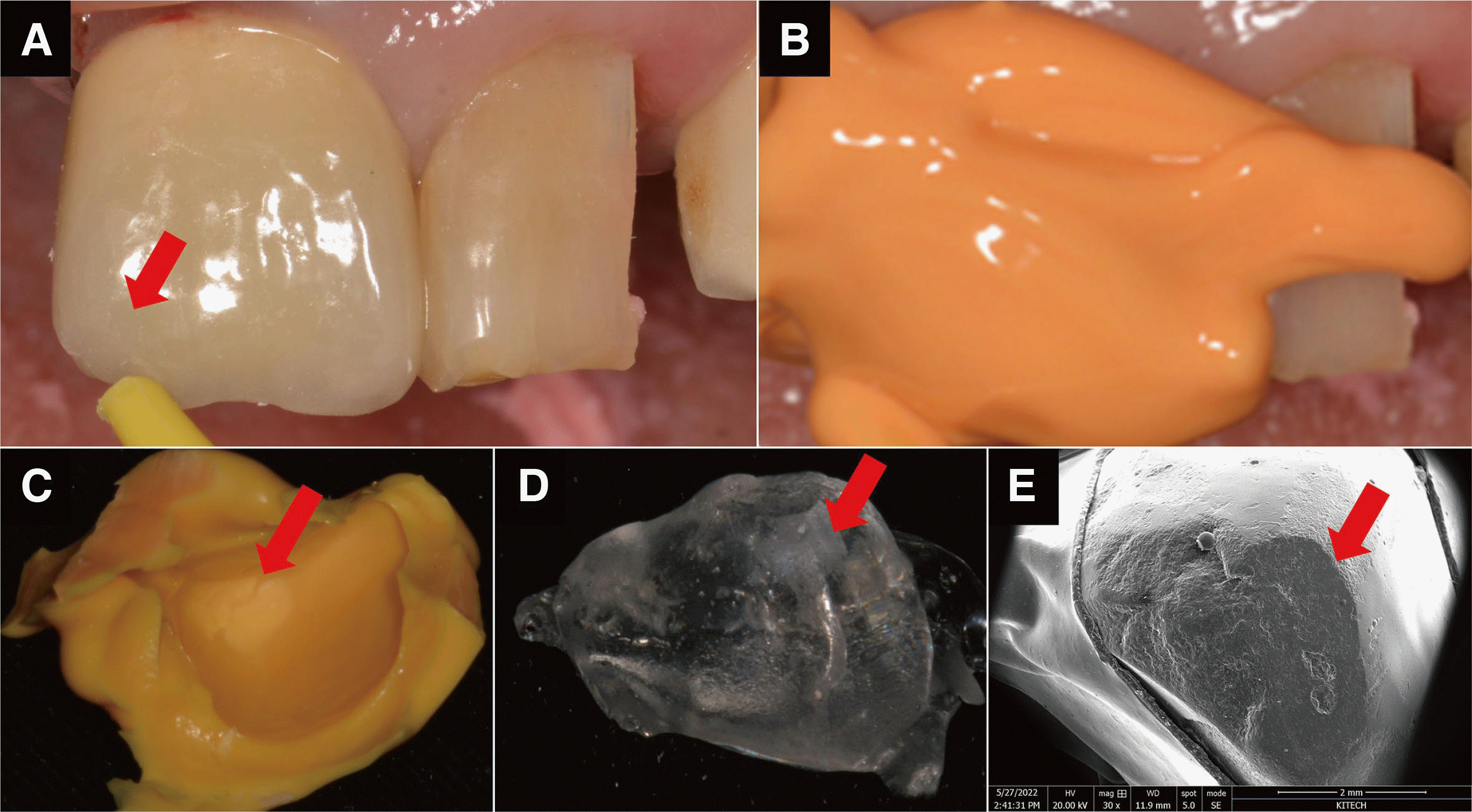
Fig. 6
Cleavage fracture. (A) Mechanism, (B) Grain structure and river pattern in fracture metal surface (red circle).
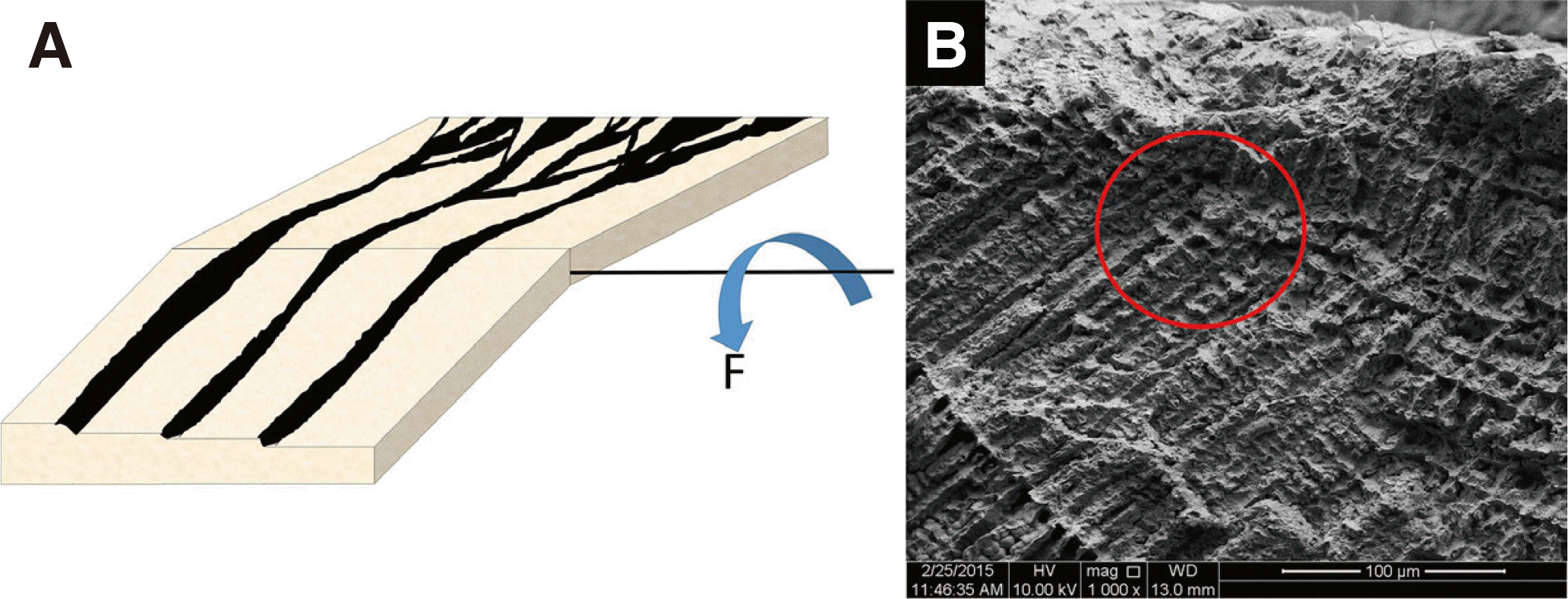
Fig. 7
Decohesive rupture. (A) Mechanism, (B) Decohesive rupture due to weak boundary of grain structure in metal fracture test (red circle).
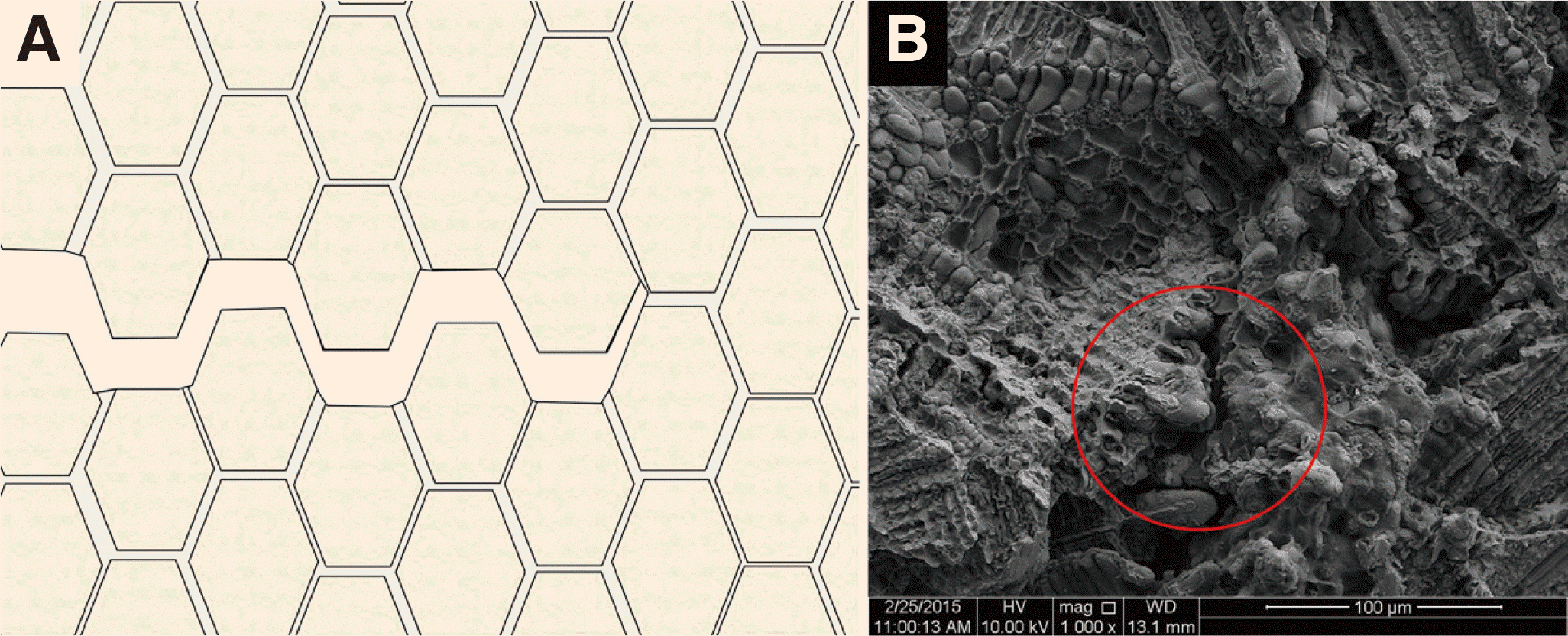
Fig. 8
Fatigue fracture of brittle materials. (A) Crack begins when the force exceeding the critical stress is applied on area where fatigue is accumulated, (B) Crack propagate to areas within the body that are most vulnerable to tensile forces, (C) During the crack propagate, tensile forces are generated perpendicular to the direction of crack propagation and chip occurs, (D) Fatigue fracture in fractured ceramic surface.

Fig. 9
Catastrophic fracture of zirconia divided into several fragments. A conchoidal fracture that occurred during the removal of a two-piece fractured zirconia prosthesis.
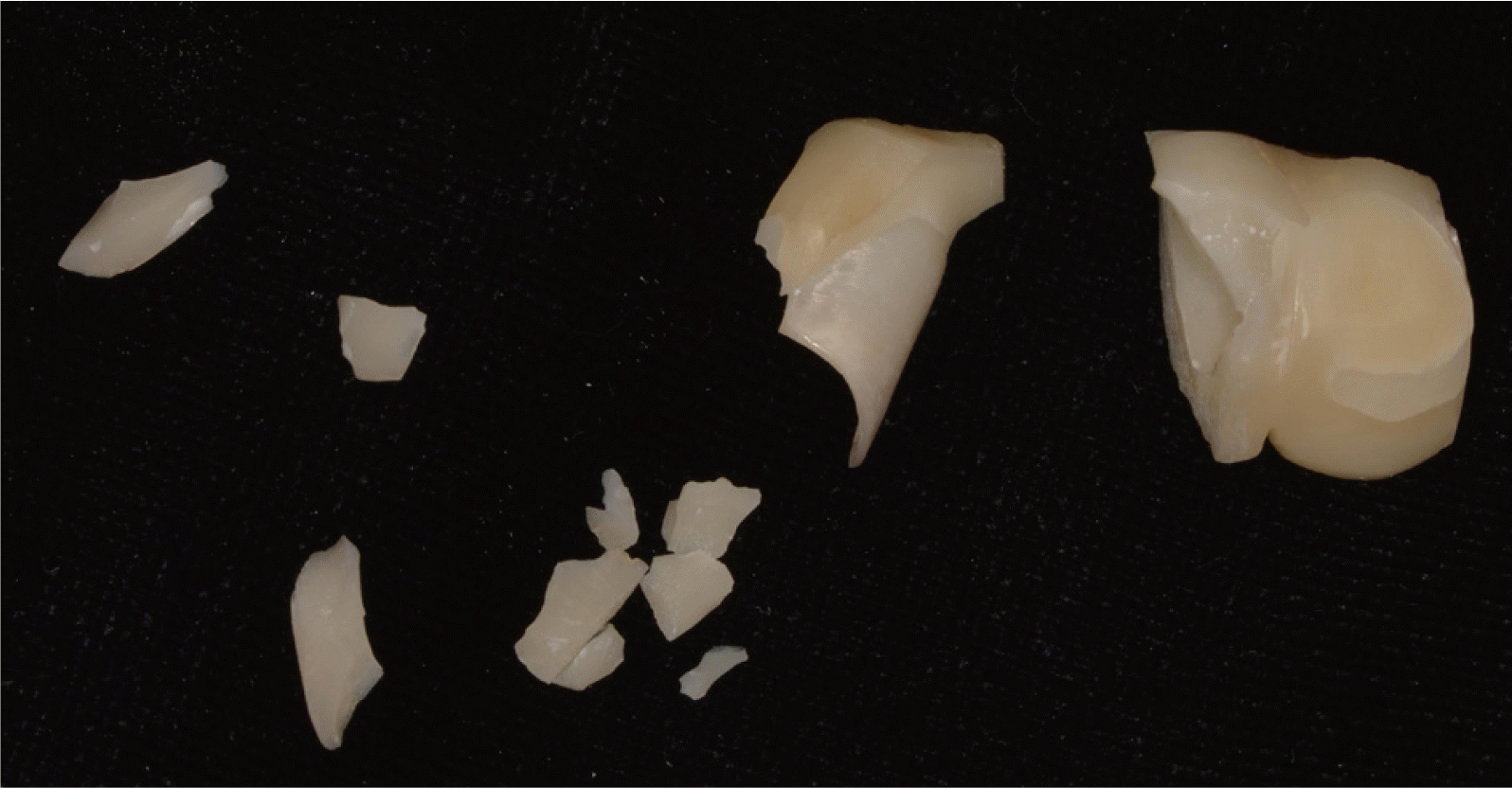