INTRODUCTION
In today's dentistry, with the developing technology and progressive material science, Computer-Aided Design/Computer-Aided Manufacturing (CAD/CAM) technique has become more popular for restorative dentistry because of many superiorities like improved conformity, homogeneity, integrity, less time- and cost-consuming production process compared to conventional techniques.
123456
In CAD/CAM processing technologies, ceramic restorations are fabricated by milling of industrial blocks. Based on the standardized industrial fabrication of these blocks, advanced physical and mechanical properties,
6789 fewer discolorations,
101112 and higher abrasion resistance
1314 can be achieved. Besides the various type of ceramic materials (feldspathic, reinforced glass ceramics, zirconia), novel ceramic blocks namely Resin Matrix Ceramics (RMC) have been also improved for CAD/CAM technique.
1516 Especially, RMC materials have been developed to combine the physical and mechanical advantages of ceramics and improved flexural properties and low abrasiveness of composite resins.
4171819 The resin nanoceramic (RNC, Lava Ultimate, 3M ESPE, St. Paul, MN, USA), polymer-infiltrated hybrid ceramic (PIHC, Enamic, Vita Zahnfabrik, Bad Säckingen, Germany), and flexible hybrid ceramic (FHC, Cerasmart, GC Corporation, Tokyo, Japan) materials are popular resin matrix ceramic CAD/CAM blocks in the markets.
171920212223 Despite their higher physical, mechanical properties and wear resistance, the RMC restorations may be weak on color reproduction and aesthetic characterization when fabricated by CAD/CAM milling process on the anterior area.
2324 Nonfunctional facial and/or incisal areas of CAD/CAM made RMC restorations will be veneered with a resin-based restorative or coating material to gain better aesthetic results.
23242526 Therefore, a combination technique for CAD/CAM made RMC restorations with an indirect resin composite (IRC) material will be suitable for this fabrication process, especially in the anterior region. This technique offers not only better mechanical properties with RMC base, but also improved, more attractive optical properties with IRC veneer supplement.
2427 However, little information is available on the bonding performance between the RMC and IRC in the case of such combination techniques.
2328 To increase the bond strength of IRC material to RMC, different surface treatments are used, such as chemical etching with hydrofluoric (HF) acid, acidulated phosphate fluoride, or phosphoric acid, airborne particle abrasion with aluminum oxide particles, tribochemical silica coating, and, in recent years, laser treatment.
22930313233 Nevertheless, there is still no definitive information about which commercially available method is suitable and effective for the bonding process of indirect resin composite to RMC.
2934
Based on these considerations, the purpose of this study was to evaluate the shear bond strength (SBS) of an IRC to the different RMC blocks using different surface treatments. The first null hypothesis was that the different surface treatment applications would not affect the SBS of an IRC to RMC blocks. The second null hypothesis was that the SBS values would not vary depending on the type of RMC materials.
Go to :

MATERIALS AND METHODS
This study evaluated the SBS of three different CAD/CAM RMC blocks (PIHC, RNC, FHC), with different surface treatment methods of conditioning for characterization with IRC. Manufacturers and material compositions are presented in
Table 1.
Table 1
Materials used in this study
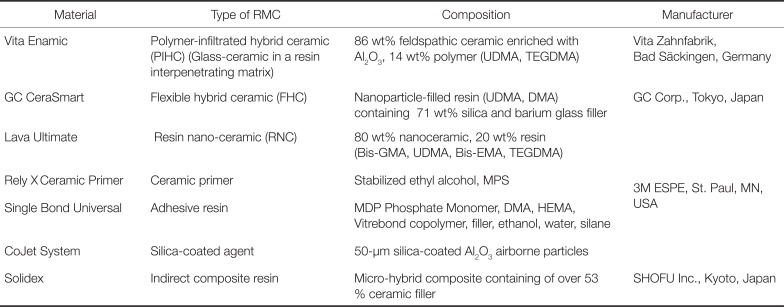
Material |
Type of RMC |
Composition |
Manufacturer |
Vita Enamic |
Polymer-infiltrated hybrid ceramic (PIHC) (Glass-ceramic in a resin interpenetrating matrix) |
86 wt% feldspathic ceramic enriched with Al2O3, 14 wt% polymer (UDMA, TEGDMA) |
Vita Zahnfabrik, Bad Säckingen, Germany |
GC CeraSmart |
Flexible hybrid ceramic (FHC) |
Nanoparticle-filled resin (UDMA, DMA) containing 71 wt% silica and barium glass filler |
GC Corp., Tokyo, Japan |
Lava Ultimate |
Resin nano-ceramic (RNC) |
80 wt% nanoceramic, 20 wt% resin (Bis-GMA, UDMA, Bis-EMA, TEGDMA) |
|
Rely X Ceramic Primer |
Ceramic primer |
Stabilized ethyl alcohol, MPS |
|
Single Bond |
Universal Adhesive resin |
MDP Phosphate Monomer, DMA, HEMA, Vitrebond copolymer, filler, ethanol, water, silane |
3M ESPE, St. Paul, MN, USA |
CoJet System |
Silica-coated agent |
50-μm silica-coated Al2O3 airborne particles |
|
Solidex |
Indirect composite resin |
Micro-hybrid composite containing of over 53 % ceramic filler |
SHOFU Inc., Kyoto, Japan |

Ninety-nine cubic specimens in dimensions of 6 × 6 × 2 mm were prepared from RMC CAD/CAM blocks under water cooling with a cutting machine (Mecatome T180, Presi Metallography, Eybens, France). The dimensions of specimens were measured by a digital micrometer (Digimatic Caliper, Mitutoyo MC, Aurora, IL, USA). The specimens that illustrate differences in size were adjusted at required dimensions. Then all specimens were embedded in autopolymerizing acrylic resin blocks (Meliodent, Heraeus Kulzer, Armonk, NY, USA). Bonding surfaces were polished under water cooling by 200, 400, and 600-grit silicon carbide papers (3M ESPE, St. Paul, MN, USA), respectively. Thereafter, all polished specimens cleaned with an ultrasonic cleaner (Erosonic Energy, Euronda, Vincenza, Italy) for 5 min in distilled water, and air-dried before surface treatments.
The RMC specimens were randomly divided into three subgroups (n = 11) according to different surface treatments. Details of the surface treatments are described in
Table 2. After the application of surface treatments, the specimens were cleaned with an ultrasonic cleaner (Erosonic Energy, Euronda, Vincenza, Italy) in distilled water for 10 minutes, and then one sample for each of the nine subgroups was examined with SEM × 2000 magnification (Nova Nano-SEM 450, FEI Comp., Hillsboro, OR, USA).
Table 2
Surface treatment groups
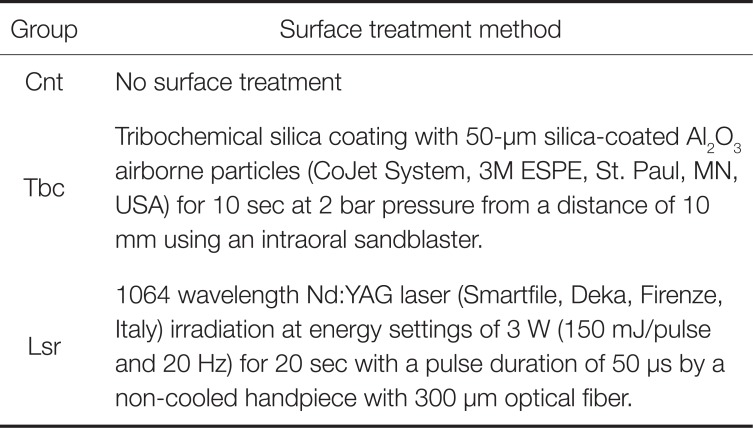
Group |
Surface treatment method |
Cnt |
No surface treatment |
Tbc |
Tribochemical silica coating with 50-μm silica-coated Al2O3 airborne particles (CoJet System, 3M ESPE, St. Paul, MN, USA) for 10 sec at 2 bar pressure from a distance of 10 mm using an intraoral sandblaster |
Lsr |
1064 wavelength Nd:YAG laser (Smartfile, Deka, Firenze, Italy) irradiation at energy settings of 3 W (150 mJ/pulse and 20 Hz) for 20 sec with a pulse duration of 50 μs by a non-cooled handpiece with 300 μm optical fiber. |

Before condensing the IRC, a methacryloxypropyltrimethoxysilane 2 (MPS) containing agent (Rely XTM Ceramic Primer, 3M ESPE, St. Paul, MN, USA) was applied onto the RMC specimens for 60 sec and lightly air-dried. Then, an adhesive material (Scotchbond Universal, 3M ESPE, St. Paul, MN, USA) was applied and light polymerization was performed using an LED light-curing unit (Blue-phase; Ivoclar Vivadent, Liechtenstein) for 20 sec. Finally, an IRC (Solidex, SHOFU Inc., Kyoto, Japan) was incrementally layered onto the treated RMC surfaces using a silicone mold with a disc-shape cavity (2 × 3 mm) to standardize the dimensions of the composite and final polymerization was performed with a light-curing unit (Solidilite V, SHOFU Inc., Kyoto, Japan), which had 4 halogen lamps to uniform polymerization in a curing time of 5 min at the wavelength spectrum of 400 – 550 nm. The application and polymerization of adhesives and composite materials were performed according to the manufacturer's instructions. All specimens were stored in distilled water at 37℃ for 24 h to allow post-polymerization. Before the SBS test, the specimens were aged with 6000 cycles of thermocycling between 5℃ to 55℃ with 30 sec dwelling time and 10 sec transfer time in distilled water.
A universal test machine (Autograph AGS X, Shimadzu Co., Kyoto, Japan) was used for the SBS test. According to the working principle of the universal test machine, specimens were placed in a special device and a moment-free axial force application at 1 mm/min crosshead speed was applied by a knife-edge shaped apparatus between the specimens and resin interface until failure occurred (
Fig. 1). The maximum load data were recorded at the time of the failure of the RMC and composite materials. The SBS was specified by dividing maximum failure load by the composite resin surface area (a= P/A=N/mm
2) and it was calculated in megapascals (MPa). After the SBS test was completed, the failure modes of all specimens were viewed by an optical microscope (MP 320; Carl Zeiss, Oberkochen, Germany) at 50 × magnification. The failure types were divided into three different categories as adhesive (between the RMC and IRC interface), cohesive (within the RMC or IRC), and mixed.
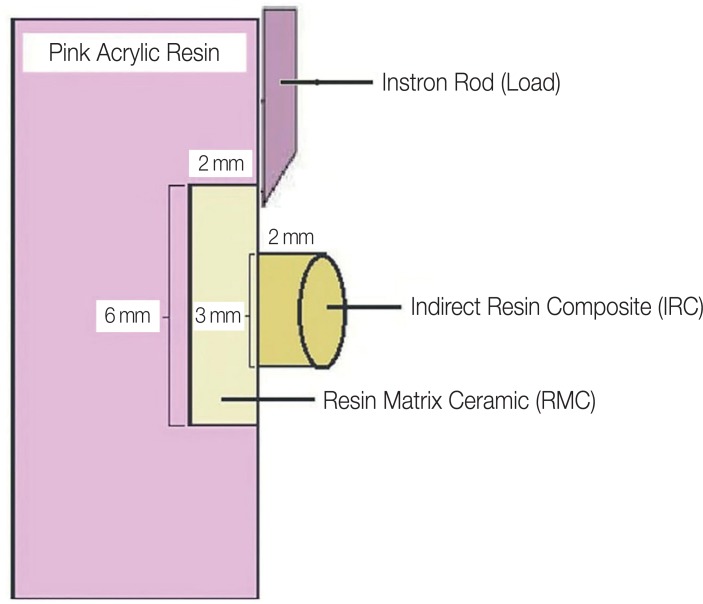 | Fig. 1Schematic view of SBS testing.
|
In the statistical analyses, the distribution of the data was evaluated using the Shapiro Wilk test and the data showed normal distribution (P = .066). Then, Levene's test of homogeneity was utilized. The SBS results were then analyzed by two-way ANOVA to assess the effects of surface treatment, RMC type, and interactions. Also, mean SBS values were compared using Tukey's multiple comparison test (α = .05). The failure modes were analyzed with Pearson Chi-Square test and the correlation between SBS and Fracture modes also compared with Kendall's tau_b correlation analyses. All calculations were performed using SPSS 20.0 V statistical software (SPSS 20.0 V, SPSS Inc., Chicago, IL, USA) and significance was evaluated at P < .05 for all tests.
Go to :

DISCUSSION
The present study evaluated the effect of different surface treatments on the SBS of an IRC material on various RMC blocks. According to the study results, the first null hypothesis that the different surface treatment applications would not affect the SBS of an IRC to RMC blocks was rejected. While the SBS values were not varied depending on the RMC materials, the second null hypothesis accepted.
The microstructure of CAD/CAM ceramic blocks influences the aesthetic properties. There are critical relations among chemical composition, fabrication process, microstructure, and aesthetic properties of CAD/CAM ceramics.
91718 The RMC materials have a composite structure that consists of both organic matrix and highly filled ceramic particles. This complex structure may provide a superior feature that allows a high degree of characterization extraorally or intraorally.
41718192034 The aesthetic outcome of CAD/CAM made RMC restorations will be questionable in the anterior region. The veneering and characterization techniques will be suitable to overcome these aesthetic problems.
22324252627282930 In the present study, the effectiveness of additional surface treatment application on the bonding performance of veneering IRC to RMC was investigated.
Until today, a wide variety of surface treatments have been used in the studies related to the SBS of resin composites to ceramic materials.
22930 In most of these studies, it has been reported that the treatment of the ceramic surface with HF acid application followed by silane coupling agent was obtained a high bond strength.
35 Chemical etching with HF acid selectively dissolves the glassy matrix of ceramic, thus creating surface microporosities and irregularities to allow the infiltration of silane coupling agent for providing micromechanical retention and chemical bonding ability with ceramic and the overlaying material.
2231 As well as positive effects of HF acid on the SBS of ceramic materials, in a study that was comparing the success of lithium disilicate, feldspathic ceramic and RNC, the researchers found that the application of HF acid to RNC could alter the surface characterization and reduce the bond strength of the materials.
22 This results may be due to the fact that the application of HF acid causes the fillers in the inorganic structure of the ceramics to detach from the material structure and thus adversely affects the bond strength.
22 Also, HF acid is toxic and caustic, and represents a potential health hazard due to its toxicity and volatility.
1535 Therefore, the questionable effects of HF acid on the bond strength of RMC, the acid roughening surface treatment protocol was not used in our study.
Airborne particle abrasion is another technique for creating a roughened surface on ceramics in prosthodontic laboratories or dental clinics. However, it can be claimed that the airborne particle abrasion surface treatment technique does not increase the micromechanical interlocking.
1535 Kern and Thompson
36 have found that sandblasting can damage material surfaces and cause a large volume loss. This result was in agreement with another study revealing that sandblasting can damage material surfaces, partially destroy the resin matrix, and expose filler particles in resin-based materials.
11 Baruticigil et al.
11 also pointed out that it may be necessary to avoid blasting ceramic restorations. Tbc technique is more suitable than airborne particle abrasion for surface treatment.
36 Tbc or silicatization using CoJet in dentistry is a commonly used successful surface treatment method for ceramic materials. This is a cold silicatization method, and this method transfers the required kinetic energy to the object material surface for the silicatization process and does not require any additional heat or light application.
3637 In addition, the CoJet system is based on airborne abrasion with especially silica-modified aluminum trioxide microblasting sand. The specific micro-blasting sand provides a reactive silica-rich treated surface. This surface structure makes the treated area suitable for the adhesion and silanization of the veneer resin material.
37 For these reasons in the present study, instead of airborne particle abrasion application, Tbc techniques with CoJet system was preferred as one of the surface treatment processes.
In the present study, it has been determined that the most effective surface treatment process for PIHC is Tbc surface treatment technique than the other RMCs. The most probable reason of this result is that the Tbc method has different effects on the bond strength of the RMCs due to the material contents. Since sand particles cannot reach the same depth in each material, the bond strength may be low on surfaces with limited sanding efficiency. In addition, the bond strength may be reduced because silicatization will be limited on surfaces where Tbc activity is limited.
32 On the other hand, PIHC material comprises a dominant ceramic network (75 vol%, 86 wt%) strengthened by an acrylic resin polymer network (25 vol%, 14 wt%) higher than other RMC materials.
16 So, the effectiveness of the Tbc method may have been greater on PIHC material than other RMCs.
4 This method can significantly increase the bond strength between PIHC surfaces and IRC by increasing the silica content on the ceramic surface.
1225
However, Tekçe et al.
38 found that the increased inorganic content of the PIHC material could lead to the formation of brittle structure than FHC. In that study, after 5000 thermal cycling, bond strength of CAD/CAM slabs from the same CAD/CAM PICH block material using dual-cure adhesive cement for 60 s to sandblasted specimens of PIHC ceramics (22.8 MPa) was significantly lower than that for 15 s (33 MPa) and also that for 30 s (35.3 MPa) specimens (
P < .001). According to these results, increasing the ceramic composition of the materials makes them undefended to the creation and propagation of cracks, and this may impair the mechanical behavior of restorative materials.
38 The results obtained by Tekçe et al.
38 and our study have varied, probably due to the difference in the veneering material, adhesive material, sandblasting time, and thermal cycling procedures.
There are some critical parameters in Tbc methods: nozzle distance from the substrate surface, impact angle to the substrate surface, working time, coverage area, and operating air pressure.
36 But generally, the manufacturers may not provide information about these parameters for sandblasting of the CAD/CAM materials that should be considered in the Tbc method. Working time varies throughout the literature.
111214 These different working time can influence the creation of surface irregularities/micro-cracks in CAD/CAM RMC blocks, and can lead to varying degrees of roughness on blocks. Therefore, Tbc application for CAD/CAM RMCs should be specific to the material.
14 In our study, PIHC samples were found to be more successful in terms of bond strength in all Tbc applied materials. This result may be due to the fact that the parameters (50-µm silica-coated Al
2O
3 airborne particles, for 10 second at 2 bar pressure from 10 mm distance of substrate surface) selected for the Tbc method are more suitable for PIHC. As in many studies,
3536 the SBS test results for FHC and RNC specimens treated with Tbc surface treatment showed a significant increase compared to the Cnt group. This success of Tbc surface treatment is thought to result from the combination of chemical roughness provided by silica and mechanical roughness provided by Al
2O
3.
36
Er:YAG (erbium: yttrium, aluminum, garnet), Nd:YAG, and Er,Cr:YSGG (erbium, chromium: yttrium, scandium, gallium, garnet) lasers have been considered as an alternative surface treatment to condition the surfaces of dental materials.
39 The laser systems work with similar mechanism and they have the capability to remove particles from surfaces by micro explosion and vaporization, a process named ablation.
3940 With this procedure, the micromechanical retention increases.
31 The wavelength of Er:YAG (2940 nm), Er,Cr:YSGG (2780 nm) and Nd:YAG (1064 nm) lasers are different from each other
3940 and these differences may lead to different surface characterization of similar materials. Kamel et al.
41 used the laser application with 2 W power, 2780 nm wave length, 20 Hz repetition rate for 20 seconds at 1 mm distance from the surface of the PIHC specimens to compare the effect of the Er,Cr:YSGG and HF acid surface treatments. According to the results of this study, it was observed that the interaction of Er,Cr:YSGG pulsed laser with the surfaces of CAD/CAM ceramic materials tested varies and this difference is related to the crystal structures of the materials used.
41 In our study, Nd:YAG laser application (3 W power, 1064 nm wave length, 20 Hz repetition rate for 20 seconds at 10 mm distance) was used for this aim. No matter the laser type and usage characteristics, in both studies, on irradiated surfaces of laser-applied PIHC samples, there was evidence of ablation and melting of the surface. Further, this surface characterization was not favorable for bonding.
41 Therefore, in our study, the Nd:YAG laser irradiation actually produced the lower SBS values for the PIHC specimens than other RMC materials. Erosion and melting were observed on the laser-irradiated PIHC surface. Fissures and cracked areas were not encountered. This result may have been due to the local temperature change caused by the non-cooled Nd: YAG laser process. Also, the non-cooled Nd:YAG laser treatment may have caused internal tensions that could damage the PIHC materials. The use of lower power of Nd:YAG laser with constant water cooling may reduce thermal side effects on PIHC materials.
36 Cengiz-Yanardag et al.
42 compared the effect of 2 W and 3 W Er,Cr: YSGG laser surface treatment (a repetition rate of 10 Hz, and 140 µs pulse duration with 55% water and 65% air for 20 sec.) on RMCs. According to the results of this study, RNCs and FHCs 2W Er,Cr:YSGG laser treated groups showed significantly lower SBS values while there was no significant difference among control, 3W Er,Cr:YSGG laser and sandblasting groups. In the same study, for RNCs 3W Er,Cr:YSGG laser group showed lower bond strength values compared to control and 2W laser groups. According to Cengiz-Yanardag et al.,
42 the low bond strengths resulting from laser surface treatment may be due to thermal surface damage caused by laser power settings. In contrast; RNCs and FHCs evaluated in our study, 3W Nd:YAG laser applied groups showed higher bond strength values compared to Cnt groups. In short, Nd: YAG lasers can be a good alternative to the surface treatment of RMCs if the most appropriate parameters are selected for each material.
The SEM images also supported the results of these SBS values by the prominent changes determined on the topographical surface of Lsr and Tbc applied RMC materials, compared to Cnt groups (
Fig. 2,
Fig. 3, and
Fig. 4). In the SEM images, it was observed that the Lsr applied surfaces had a large number of defects and retentive area. These findings will be interpreted that the Lsr treated surfaces are able to provide more retentive surface than Cnt groups. In other word, these results indicated that Lsr surface treatment increases the initial bond strength between the IRC and RMC.
Surface treatment methods lead to partially destroying the resin matrix and exposing filler particles to resin-based materials such as IRC.
27 Silanization is indispensable to provide a resistant bonding after the above-mentioned surface treatment options. Thus, a better mechanical interlocking between treated surface and substrate may be achieved.
28 The present study supported this idea, and it has been showed silane coupling agent application to the treated ceramic surface results in significant bonding between the IRC and RMC materials. Both the Lsr and Tbc specimens showed superior initial as well as durable SBS compared to the Cnt groups. The possible reason for this finding is that a strong chemical bonding is formed between the silane and the silica in the treated ceramic surface by means of a siloxane network.
25 For our study, this reasoning explains the higher prevalence of cohesive failures, especially in the Lsr treated ceramic specimens.
In a study that tested similar materials with the µSBS test method, Cengiz-Yanardag et al.
42 reported that the most common type of fracture in Lsr and Tbc treated specimens were adhesive fracture. But, in the current study, there were no adhesive - mix failures in Lsr and mix failure in Tbc groups. These findings mean that the bond strength of the IRC to ceramics exceeds the shear bond strength between the ceramic and the IRC. Also, these findings demonstrated that ceramic surface treatment with Lsr or Tbc is an effective method to improve SBS to RMC. The observation of cohesive failure may lead to the conclusion that the adhesion of IRC to the ceramic, regardless of its surface treatment, is sufficient within the limits of this study.
There is no definitive threshold bond strength value of veneering materials to RMC that can be regarded “clinically acceptable”. However, a clinically acceptable threshold of bond strength ranges for resin to ceramics was reported between 10 and 13 MPa.
1543 In the present study, the bond strengths of all specimens were 17 MPa in average, so veneering of RMC with IRC seemed clinically acceptable method for ceramic characterization.
Nevertheless, the occurrence of cohesive failures can also be attributed to the bond test employed. Many studies that used SBS tests observed that this methodology often produces fracture away from the adhesion zone and may increases the likelihood of cohesive or combined fractures. Moreover, the incidence of cohesive fractures may be increased due to the nonhomogeneous stress distribution along the bonded interfaces in the SBS test procedure.
3944 This nonhomogeneous interface stress distribution causes fractures to start from defective areas in the interface or material that exhibit high-stress concentration. Therefore, in the present study, regardless of the surface treatments applied to the ceramic, the type of fracture was mostly cohesive.
The design of this
in vitro study has several limitations, so the results of this study should be carefully evaluated. One of the limitation of this study is that the SBS test has been widely used for
in vitro investigations of resin ceramics, but it has some limitations about the uniform stress distribution across the material.
41535 Another limitation is the simplified specimen design. This design allows for some basic bonding assessments under standardized and controlled conditions, but cannot simulate the complex interactions between the three-dimensionally shaped frameworks and veneering materials. The bond strength of different types of IRC materials to RMC should be evaluated in further
in vitro and
in vivo studies using various surface treatments, different Nd:YAG laser irradiation time and power settings, different adhesive materials, and different adhesive systems. Also, the validity of using IRC as veneering or characterization materials to RMC should be confirmed in randomized clinical research.
Go to :
