This article has been
cited by other articles in ScienceCentral.
Abstract
Objectives
There has been a growing interest in glass ceramic systems with good esthetics, high fracture resistance and bonding durability, and simplified fabrication techniques using CAD/CAM. The aim of this study is to compare flexural strength before and after heat treatment of two lithium disilicate CAD/CAM blocks, IPS e.max CAD (Ivoclar Vivadent) and Rosetta SM (Hass), and to observe their crystalline structures.
Materials and Methods
Biaxial flexural strength was tested according to ISO 6872 with 20 disc form specimens sliced from each block before and after heat treatment. Also, the crystalline structures were observed using field-emission scanning microscopy (FE-SEM, Hitachi) and x-ray diffraction (XRD, Rigaku) analysis. The mean values of the biaxial flexural strength were analyzed by the Mann-Whitney U test at a significance level of p = 0.05.
Results
There were no statistically significant differences in flexural strength between IPS e.max CAD and Rosetta SM either before heat treatment or after heat treatment. For both ceramics, the initial flexural strength greatly increased after heat treatment, with significant differences (p < 0.05). The FE-SEM images presented similar patterns of crystalline structure in the two ceramics. In the XRD analysis, they also had similar patterns, presenting high peak positions corresponding to the standard lithium metasilicate and lithium disilicate at each stage of heat treatment.
Conclusions
IPS e.max CAD and Rosetta SM showed no significant differences in flexural strength. They had a similar crystalline pattern and molecular composition.
Go to :

Keywords: Biaxial flexural strength, CAD/CAM restoration, Crystalline structure, Lithium disilicate glass ceramic
Introduction
There has been growing interest in glass ceramic systems due to their good esthetics, excellent fracture resistance to occlusal forces, bonding durability between the prepared tooth surface and ceramic, and simplified fabrication techniques using computer-aided design/computer-aided manufacturing (CAD/CAM). In the early 90's, IPS Empress 1 (Ivoclar Vivadent, Schaan, Liechtenstein), a leucite-reinforced glass ceramic was launched in the dental market. The finely dispersed leucite crystals in the amorphous glass matrix increased the strength by suppressing crack propagation and enhanced clinical performance.
1 Thereafter, IPS Empress 2, which is a lithium disilicate glass ceramic mainly composed of quartz, lithium dioxide, phosphor oxide, alumina oxide, and potassium oxide, was introduced by the same manufacturer. In 2001, this manufacturer released IPS e.max Press, which is a castable lithium disilicate glass ceramic with the improvement of mechanical and optical properties. Four years later, IPS e.max CAD was introduced for CAD/CAM restoration in the dental clinic.
CAD/CAM technology has enabled dental clinicians to restore teeth using ceramic material in a single appointment.
2 First, partially crystalized ceramic block can be milled and shaped by computer. During a post-milling heat treatment, the fabricated ceramic restoration can achieve full density and increased strength. At the same time, the initially bluish color changes to a tooth-like shade with improved translucency and brightness. While alumina- or zirconia-based ceramic cores require additional porcelain layering for esthetic enhancement, lithium disilicate glass ceramic has superior optical properties by itself. Therefore, the lithium disilicate ceramic block can be milled to the final contour, with only a staining procedure added to provide a more realistic tooth appearance. This mono-compound fabrication technique has a major advantage, considering that the most frequently encountered complication of all-ceramic restoration is chipping of the veneering porcelain.
3
The second most frequent contributor to clinical failure may be bulk breakdown of the restoration.
4 Ceramics are inherently brittle materials and prone to breaking under inadvertent bending forces. In intraoral circumstances, restorations should attain a strength sufficient to withstand repeated masticatory force. Flexural strength commonly represents the capacity to tolerate chewing force.
5 The structure of monolithic lithium disilicate can resist masticatory stress, dissipating it throughout the entire restoration. The even distribution of stress without concentration sites is crucial in clinical outcomes, since the failure stresses of ceramics are closely related to not only surface flaws and porosities but also internal disintegration.
6
The lithium disilicate ceramic block for CAD/CAM restoration in the dental clinic was exclusively available from a single manufacturer as mentioned above. Recently, another lithium disilicate ceramic block (Rosetta SM, Hass, Gangneung, Korea) was released. In this study, the flexural strength of the two commercially available lithium disilicate CAD/CAM blocks was compared before and after heat treatment. In addition, the crystalline structures of the two lithium disilicate ceramics were observed using field-emission scanning microscopy (FE-SEM) and x-ray diffraction (XRD) analysis. The null hypothesis was that the two lithium disilicate glass ceramics would not differ in their physical properties based on flexural strength and crystalline structure.
Go to :

Materials and Methods
Specimen preparation
For the specimens of Groups A and B (
Table 1), five partially crystallized blocks of each of IPS e.max CAD and Rosetta SM were ground to cuboidal form using a Horizontal Rotary Grinding Machine (HRG-150, AM Technology, Asan, Korea) and then milled to cylindrical form of the diameter of 12.0 mm using a Tool Grinder (C-40, Sungkwang Machinery, Siheung, Korea). Another five partially crystallized blocks of each of IPS e.max CAD and Rosetta SM were ground and milled to cylindrical form of the diameter of 12.1 mm to compensate for shrinkage (0.2 - 0.4%, according to the manufacturers) during heat treatment for the specimens of Groups C and D (
Table 1). Those cylinders were sliced into discs using a diamond saw. Each disc was finely ground to a 1.20 mm thickness for the specimens of Groups A and B, and to a 1.21 mm thickness for Groups C and D using a #320 MESH diamond wheel. They were polished using slurry in the order of 6, 3, and 1 µm diamond grit in a lapping machine (SPL-15, Okamoto Corp., Yokohama, Japan). The discs of Groups C and D were heat-treated in a press furnace (RPF 12, Hass) according to the manufacturer's instructions (
Table 2). Finally 20 specimens per group were obtained.
Table 1
Materials used and group categorization

Table 2
Crystallization parameters for post-milling heat treatment

Measurement of biaxial flexural strength
The piston-on-three-ball test was used to measure the biaxial flexural strength (
Figures 1a and 1b). Specimens were centered and supported on three symmetrically spaced balls. The diameters of the piston tip and the support circle were 1.2 and 10.0 mm, respectively. A load was applied at the center of the specimen through the flat tip of the piston at a cross-head speed of 1.0 mm/min in air at room temperature using a universal mechanical testing machine (Instron 4202, Canton, MA, USA). A thin plastic film (50 µm in thickness) between the piston and the upper surface of the specimen was used to distribute the load uniformly.
7
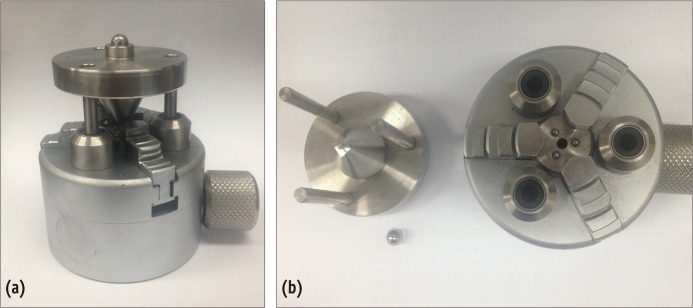 | Figure 1Fixture with a piston-on-three-ball set up according to ISO 6872. 
|
The biaxial flexural strength was calculated using the following equation:
where σ is the maximum center tensile stress and P is the total load at fracture.
8
in which v is Poisson's ratio, r
1 is the radius of the support circle, r
2 is the radius of the loaded area, r
3 is the radius of the specimen, and b is the specimen thickness at the fracture origin. Poisson's ratio was taken to be 0.25, the standard value for conventional ceramics.
8
Microscopic observation of crystalline structures
For each group, 3 specimens were chosen according to their flexural strength value: close to maximum, minimum, and average for their group. One fractured fragment from each of those specimens was selected to be observed by FE-SEM. For the specimens in Groups A and B, etching was done with 3% HF for 3 seconds. For the specimens in Groups C and D, etching was done with a mixture of 3% HF and 30% H2SO4 for 30 seconds. After etching and platinum coating, microscopic images were obtained from FE-SEM.
Molecular identification of crystals
The other fractured segment from the same specimen used for the FE-SEM was subjected to XRD analysis. The specimens were placed in the holder of an XRD and scanned using CU Kα x-rays at a diffraction angle from 10 to 80 degrees with a scanning speed of 5°/min, 40 Kv, and 60 mA. The reference data for the interpretation of the XRD patterns were obtained from the XRD standards file index, Joint Committee on Powder Diffraction Standards (JCPDS).
Statistical analysis
The mean values of the biaxial flexural strength were analyzed by a Mann-Whitney U test at a significance level of p = 0.05. The analyses were performed using IBM SPSS Statistics 20.0 (IBM Corp., Armonk, NY, USA).
Go to :

Results
The mean values of biaxial flexural strength in megapascals (MPa) for all of the groups are shown in
Table 3. There were no statistically significant differences in flexural strength between the IPS e.max CAD and Rosetta SM either before heat treatment or after heat treatment. For both lithium disilicate ceramics, the initial flexural strength had greatly increased after heat treatment, with significant differences (
p < 0.05).
Table 3
Biaxial flexural strength of the two lithium disilicate glass ceramics before and after heat treatment (Mpa)

The FE-SEM images revealed similar crystalline structure patterns in the two lithium disilicate ceramics (
Figure 2). The IPS e.max CAD showed typical lithium metasilicate crystals embedded in a glass matrix. The typical platelet-shaped grains had a length of approximately 0.5 µm. The Rosetta SM had crystals resembling the shapes and sizes of those of IPS e.max CAD. After heat treatment, the crystalline microstructure changed into a more dense form, and the size of the crystals increased up to 2.0 - 3.0 µm (Group C) and 1.0 - 2.0 µm (Group D).
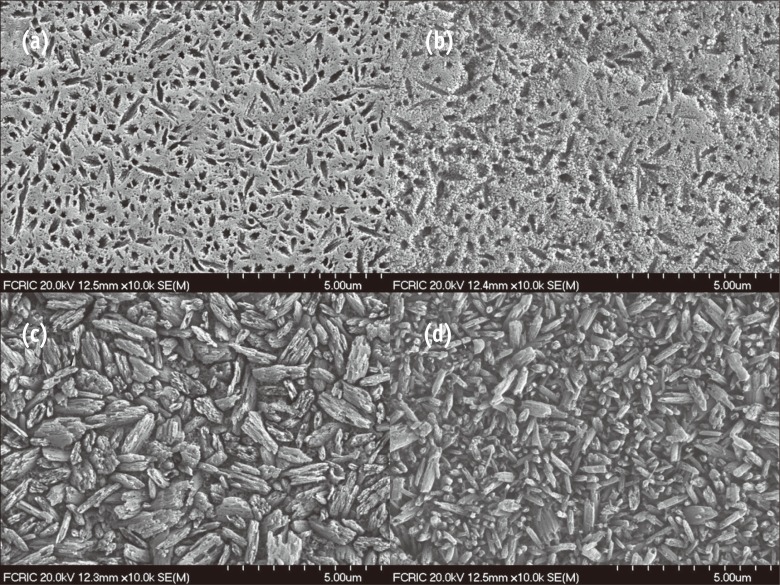 | Figure 2Field-emission scanning microscopy (FE-SEM) micrographs of fractured surfaces after biaxial flexural test (×10,000). Both ceramics display similar patterns of crystalline structure before heat treatment (upper micrographs) and after heat treatment (lower micrographs). (a) Microstructure of IPS e.max CAD in lithium metasilicate crystalline form; (b) Rosetta SM in lithium metasilicate crystalline form; (c) IPS e.max CAD in lithium disilicate crystalline form; (d) Rosetta SM in lithium disilicate crystalline form. 
|
In the XRD analysis, the IPS e.max CAD and Rosetta SM also had similar patterns, presenting high peak positions corresponding to the standard ones for lithium metasilicate and lithium disilicate at each stage of heat treatment (
Figure 3). The intensities of radiation were also similar in the two products. JCPDS references are shown below the XRD results.
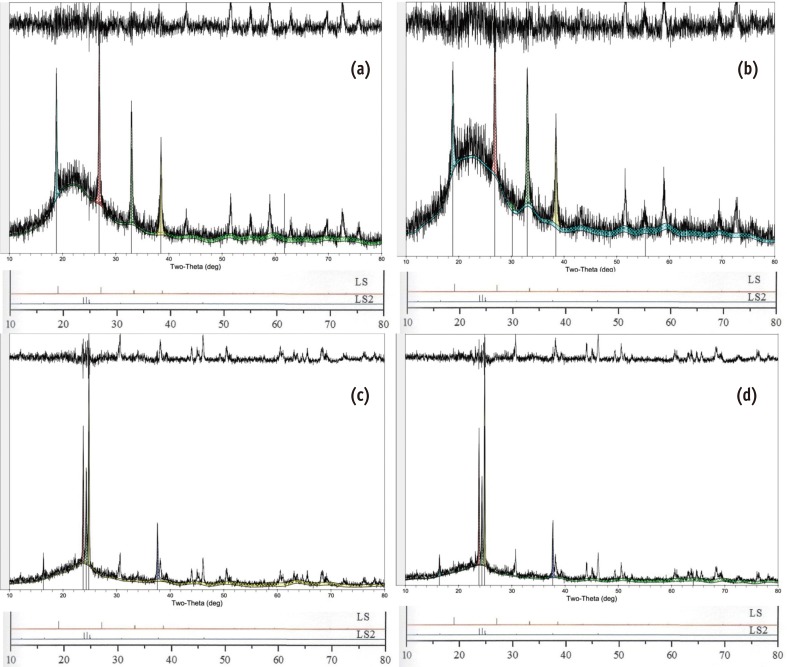 | Figure 3X-ray diffraction (XRD) patterns of IPS e.max CAD (a) and Rosetta SM (b) before heat treatment show high peaks at the locations denoting standard pure lithium metasilicate (JCPDS 29-0829). After heat treatment, the high peak positions in the XRD diagrams of the IPS e.max CAD (c) and Rosetta SM (d) are in agreement with those of standard pure lithium disilicate (JCPDS 15-0637). 
|
Go to :

Discussion
Currently, several types of ceramic materials such as leucite-reinforced glass ceramic, lithium disilicate glass ceramic, and zirconia-based core ceramic have been utilized for chair-side fabrication of all-ceramic restorations using CAD/CAM.
2 Lithium disilicate glass ceramic maintains a relatively high strength, which is high enough for full-coverage crowns in the posterior area. The ceramic blocks are partially crystallized and contain both lithium metasilicate (Li
2SiO
3) and lithium disilicate (Li
2Si
2O
5) crystal nuclei. In this state, the milling burs are readily applicable with minimized wear-out, also allowing the restorations to be cleanly machined without chipping. After the machined ceramic is processed under post-milling sintering, its flexural strength exceeds that of conventional feldspathic porcelain or leucite-reinforced glass. To state the strength of ceramic materials definitively seems infeasible due to the multiple factors influencing measurements, such as the testing method, specimen dimensions, test environment, polishing procedures, stress rates, and stress area.
9 Our data obtained from IPS e.max CAD were relatively higher than the values claimed by the manufacturers. It has been reported that the biaxial flexure test tends to yield higher values than the 3-point flexure test.
10 Our data were close to the results reported by Buso et al. and Lin et al. [mean flexural strength (SD) of 416.1 (50.1) MPa and 365.1 (46.0) MPa], which had been obtained from specimens of a similar size and shape to ours and by a similar method.
3,
11 Rosetta SM also had a similar flexural strength value to IPS e.max CAD. Also, the strengths of the two lithium disilicate ceramics were not significantly different before the heat treatment. This is noteworthy, since the initial strength of the block may be related to the risk of crazing and crack formation during the milling process.
12,
13
For lithium disilicate ceramics, the heat treatment required for final crystallization takes no longer than 25 minutes.
14 This short firing time is a major advantage in a single visit treatment. On the other hand, a zirconia core machined by CAD/CAM requires 6 to 8 hours for post-milling processing time.
15 The extended duration of the post-milling process may often discourage the delivery of the restoration within the same day. Furthermore, even with the outstanding flexural strength (approximately 1,000 MPa) of a zirconia core, the inferior mechanical properties of the veneering porcelain make the bi-layer ceramic restoration prone to chipping or fracture, resulting in significant clinical failure.
16,
17
The two lithium disilicate glass ceramics tested in this study produced similar SEM images before and after heat treatment. In the heat-treated groups, HF and H
2SO
4 acid etching eliminated the glass matrix, exposing the embedded crystal particles. The platelet-shaped crystals were homogeneously dispersed in an interlocking network, which is common for the two lithium disilicate glass ceramics. The densely packed crystalline structure can hinder crack propagation and increase mechanical strength. Even if cracks were to form, they would become trapped within the crystals in a more circuitous manner, potentially preventing further propagation.
9 In this study, Group C showed crystals that were larger than those of Group D. However, even in the same product, the crystals can vary in size according to the shade or opacity. Their size depends on the base glass composition, nucleating agents, and heat treatment among other factors.
18
As the XRD results showed, the main components of Rosetta SM were identical to those of IPS e.max CAD. Not only the main peak locations specifying the main crystals, lithium metasilicate and lithium disilicate, but also the background intensities were similar to each other. Therefore, our null hypothesis was entirely confirmed.
Several other properties are required for dental ceramics to fulfill clinical expectations. Among them are the elastic modulus, thermal expansion coefficient, fracture toughness, surface hardness, color, and translucency. Additional studies are needed to evaluate those properties.
Go to :

Conclusions
Based on the results from this in vitro study, the two lithium disilicate glass ceramics for CAD/CAM restoration in the dental clinic showed a similar flexural strength, crystalline pattern, and molecular composition. Clinicians may extend the selection of materials for chair-side glass ceramic restorations using CAD/CAM to include either of these lithium disilicate glass ceramics among their options.
Go to :
