Quality control phantom
A phantom model, referred to as CQP-IFBA, was created in polymethyl methacrylate (PMMA) based on the CQ-01-IFBA prototype developed by Dr. Wilson Batista. This cylindrical phantom, 70 mm high and 150 mm in diameter, is of modular design and divided into 7 circular discs of PMMA (10 mm high and 140 mm in diameter). The phantom consists of different materials that represent structures with various densities, allowing image quality parameters to be evaluated. The phantom structure was elaborated according to the image quality parameters, as presented in
Table 1.
Table 1
Image quality parameters and structure of phantom CQP-IFBA

To ensure that disc rotation did not occur, black disc marks were performed with a radiotransparent material (
Fig. 2A). A docking slot was created in all the small discs disposed inside the regular discs to avoid disc rotation (
Fig. 2B). Two black vertical landmarks were also defined to ensure that the phantom was aligned according to the CBCT laser positioners, since for optimal performance, it is essential to correctly position the phantom.
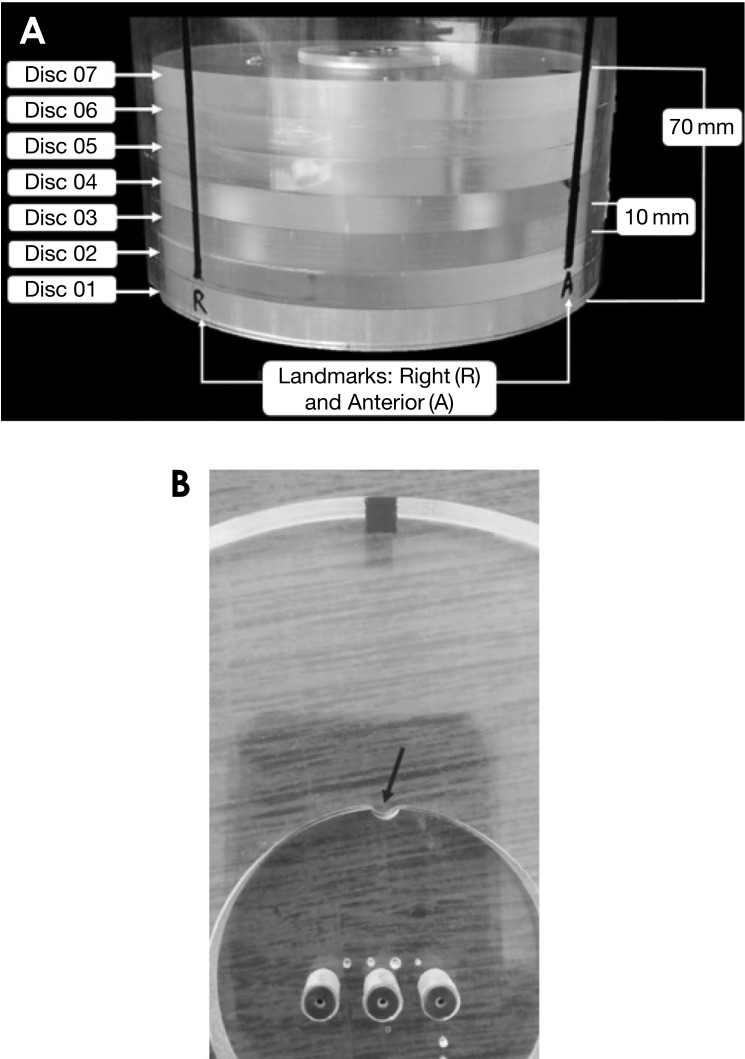 | Fig. 2Design of the phantom CQP-IFBA. A. Seven discs and location landmarks, B. docking slot inside the regular discs
|
At the bottom of the phantom, disc 1 allowed the evaluation of geometric accuracy via the measurement of distances between the micro-holes. Disc 2 was a homogeneous PMMA disc (without drilling or landmarks), used to evaluate the image noise and uniformity. Disc 3 had a hole with air placed in the center of the PMMA disc. Further, disc 4 contained 5 elements with different densities placed in the periphery and the center of the disc: polyvinylchloride (PVC), polytetrafluoroethylene (PTFE), nylon, Delrin (polyoxymethylene), and polypropylene (PP). The rods inserted were 15 mm in diameter and 10 mm high. Both discs 3 and 4 were used to assess the contrast-to-noise ratio (CNR) and the signal-to-noise ratio (SNR). However, when the exposure protocol or CBCT unit had a small FOV (≤100 mm), only the centered rods were used. Disc 5 allowed the evaluation of the spatial resolution (5 line pairs/cm [lp/cm] to 16 lp/cm) by the bar pattern. Low-contrast assessment was evaluated with disc 6. In this disc, 7 rods of PP with diameters of 7 mm, 6 mm, 5 mm, 4 mm, 3 mm, 2 mm, and 1 mm, all 10 mm high, were inserted into the PMMA disc. In the upper part of the phantom, disc 7 was used to evaluate the artifact index. This final disc had a small disc inserted (50 mm in diameter and 10 mm in height) with 3 titanium implants (5 mm in diameter and 10 mm in height) to produce the metallic artifacts. The implants were located in the same plane and in parallel.
CBCT phantom acquisition was performed using 3 different CBCT scanners: NewTom™ 5G (QR srl, Verona, Italy), Cranex® 3D (Soredex Oy, Tuusula, Finland), and Scanora 3D (Soredex Oy, Tuusula, Finland). The experimental tests were conducted according to the exposure parameters available in each device, with current and optimized protocols.
To ensure that the phantom was correctly positioned within the FOV, before the phantom acquisitions, a scouting view was performed. A single scan was sufficient to include the whole phantom. The images were exported and viewed using ImageJ version 1.49e (National Institutes of Health, Bethesda, MD, USA).
Phantom-dedicated software
The CBCT quality assurance (QA) software was developed on ImageJ (National Institutes of Health, USA), to analyze image quality. After the phantom image acquisitions, Digital Imaging and Communication on Medicine (DICOM) images were opened in the ImageJ software and the user identified the directory where the images were saved. The DICOM header was read to identify the manufacture, the number of images, the voxel size (mm), FOV (mm), tube voltage (kV), tube current (mAs), exposure time (ms), and dose area product (mGy·cm2). Information from the equipment manufacturer indicated the image acquisition range orientation (top to bottom, or bottom to top).
After this procedure, the macro created an 80-mm circular region of interest (ROI) in all the image centers to identify the highest standard deviation pixel value, which corresponded to disc 03, which had a hole inside, with the air corresponding to the lowest pixel value. Based on the automatic image selection of disc 03, the positioning of the phantom was verified based on a square ROI; that is, analyzed using rectangular vertical and horizontal ROIs to identify the greatest standard deviation. The square ROI definition was based on the central part of the phantom, considering the vertical number of pixels, divided by 3 (
Fig. 3).
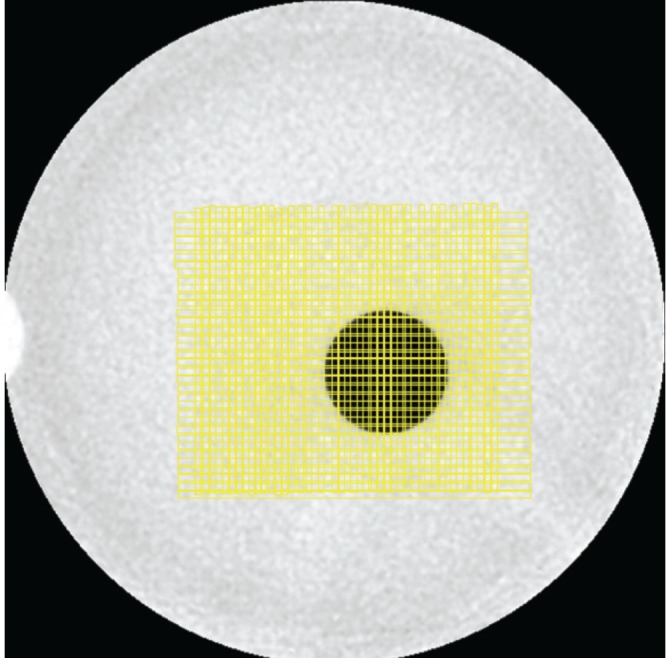 | Fig. 3Rectangular ROIs (vertical and horizontal) are drawn to identify highest standard deviation on disc 3.
|
If the phantom was not well positioned according to the isocenter, the position of the ROI was automatically corrected in the image. Based on the result of the maximum standard deviation of the ROI, the center of the image was identified by its coordinates in the x- and y-axes. Thus, this automatic process reduced variability due to the lack of operator skill or the observer's experience in handling of the phantom. After the identification of disc 3, the best image per disc was selected in the order presented in
Table 2.
Table 2
Methods automatically defined to select the best image per disc

An image for each of the 7 discs was selected, meaning that 7 images were evaluated in total. The ROIs used for image quality analyses were created in the same points of interest in the phantom based on the matrix and voxel size previously detected on the DICOM header. This allowed the software to be adapted to different manufacturers.
ROIs for image quality analysis were automatically defined based on image coordinates from the known distances of structures on the phantom. The image quality parameters evaluated were: SNR, CNR, image uniformity, image noise, geometric accuracy, spatial resolution, low-contrast resolution, and the artifact index. The methods are described below.
To evaluate the SNR, 6 circular ROIs (diameter, 8 mm) were placed in 6 elements of different densities: PTFE, PP, nylon, Delrin, air, and PMMA. These elements represented the signal response of different structures. The macro obtained the SNR values as:
The CNR was evaluated using PTFE, PP, nylon, Delrin, air, and PMMA. A circular ROI (diameter, 8 mm) was drawn in the center of each material. For FOVs smaller than 100 mm in diameter, only the centered objects placed in disc 4 were evaluated. However, the air was evaluated using disc 03. The CNR value was calculated as:
where
Signalmaterial is the mean pixel value of the material;
SignalPMMA is the mean pixel value of the background (PMMA),
SDMaterial is the standard deviation of the material, and
SDPMMA is the standard deviation of the background.
Low-contrast resolution is related to the ability to discriminate structures with slight differences in attenuation properties. Low-contrast resolution is commonly expressed as the minimum detectable size of an image structure relative to the contrast background. Low contrast was obtained through disc 6, on which 7 ROIs, 5 mm in diameter, were constructed in each polypropylene rod. The polypropylene rods had diameters of 7 mm, 6 mm, 5 mm, 4 mm, 3 mm, 2 mm, and 1 mm, with heights of 10 mm. Another ROI placed on PMMA, with the same dimensions (5 mm) and the same slice, was used to represent the background values. Low-contrast assessment was performed using polypropylene and a PMMA background and calculated using the CNR (Equation 2). Polypropylene has subtle differences from PMMA, making this arrangement suitable for representing low-contrast resolution.
The image noise was evaluated from the application of circular ROIs (diameter, 30 mm) corresponding to one-fifth of the phantom diameter (Equation 3). These ROIs were positioned in the center of disc 2. Noise was considered as the standard deviation from the average value in 5 consecutive axial sections and calculated as:
The geometric accuracy was obtained from the known values of the distances between the micro-holes, which were measured and compared with known distances (10 mm), both vertically and horizontally.
The spatial resolution was evaluated by the bar pattern (5 lp/cm to 16 lp/cm) located in disc 5. A linear ROI in the center of the bar pattern was plotted, and a graph representing the spatial resolution was constructed.
Image uniformity was evaluated using the pixel intensity measurements obtained from disc 02. ROIs (diameter, 10 mm) were placed around the periphery, and also in the center (1 ROI) of the PMMA. The measurements were made in a transaxial slice and calculated using:
where
Max is the maximum mean pixel intensity of the disc 5 ROIs and
Min is the minimum value of the mean pixel intensity of the ROIs.
The artifacts were measured on disc 7 of the phantom, and the mean pixel value in PMMA was obtained without the presence of metallic objects. The value of the pixel intensity from disc 7 was subtracted from the blank PMMA, and only pixels with a high signal from the metallic artifact were shown. Two ROIs were drawn around the implants, and the mean values of the adjacent exposed metal objects were obtained. The artifact index was measured as:
where
MPART and
MPPMMA are the mean pixel values in the adjacent area of the rods and PMMA, respectively.
The metallic objects produced higher values than the PMMA; thus, a higher artifact index value was attributed to a greater contribution of the metallic artifacts.
Finally, a report was generated containing the results and an analysis of the information. In addition to quantitative information regarding image quality indicators, exposure parameters, dose area product (DAP), and the next date for quality control tests were also presented.
The results can be exported for further processing as graphical plots. The program can run independently of the operating system and has the possibility to add new functions.