Abstract
Objective
The purpose of this study was to evaluate the surface roughness (SR) of 2 types of orthodontic archwires made by 4 different manufacturers.
Methods
This in vitro experimental study was conducted on 35 specimens of 7 different orthodontic archwires, namely, 1 nickel-titanium (NiTi) archwire each from the manufacturers American Orthodontics, OrthoTechnology, All-Star Orthodontics, and Smart Technology, and 1 stainless steel (SS) archwire each from the manufacturers American Orthodontics, OrthoTechnology, and All-Star Orthodontics. After analyzing the composition of each wire by energy-dispersive X-ray analysis, the SR of each wire was determined by scanning electron microscopy (SEM) and surface profilometry. Data were analyzed using the Kruskal-Wallis and Mann-Whitney U tests (α < 0.05).
Results
The average SR of NiTi wires manufactured by Smart Technology, American Orthodontics, OrthoTechnology, and All-Star Orthodontics were 1,289 ± 915 A°, 1,378 ± 372 A°, 2,444 ± 369 A°, and 5,242 ± 2,832 A°, respectively. The average SR of SS wires manufactured by All-Star Orthodontics, OrthoTechnology, and American Orthodontics were 710 ± 210 A°, 1,831 ± 1,156 A°, and 4,018 ± 2,214 A°, respectively. Similar to the results of profilometry, the SEM images showed more defects and cracks on the SS wire made by American Orthodontics and the NiTi wire made by All-Star Orthodontics than others.
Archwires are the most important parts of commonly used orthodontic appliances.1 The surface roughness of orthodontic arch wires is an essential factor in determining the effectiveness of archwire-guided tooth movement, corrosion behavior, surface contact and friction, biocompatibility, esthetics, hygiene, and color stability of archwires.2-4 Corrosion and surface roughness of archwires and ion release in the oral environment are reported to be positively correlated.1 Increased surface roughness can increase frictional forces because it enhances the contact area between the bracket and the wire. This can, in turn, reduce the orthodontic force by 50% or more,2,3,5-7 thereby lowering the quality of orthodontic treatment.3,5,6,8 Further, recent studies have shown that when a correction of greater than 3 mm is attempted for a misaligned tooth, the elimination of friction is very important to ensure the quality of orthodontic treatment.9
Nickel-titanium (NiTi) and stainless steel (SS) alloys are the commonly used materials for the fabrication of orthodontic archwires.2-5 The roughness and irregularity of the surface of archwires are positively correlated with their corrosion behavior.2-5 Widu et al.10 have shown that surface roughness can serve as an indicator of the tendency of orthodontic wires to corrode. Oshida et al.11 reported that the defects introduced during the manufacturing process of NiTi wires are areas susceptible to corrosion.
Metal ion release caused by corrosion is a source of concern among researchers and clinicians because it can have known and unknown effects on the human body; it can affect the oral mucosa, immunological system, and biological functions, leading to contact allergy and probably systemic disturbances.12-15 The SS and NiTi alloys contain high ratios of metals with allergenic and sometimes carcinogenic and cytotoxic effects (e.g., nickel).12,13 Considering this property of the alloys and the fact that surface roughness affects frictional forces and metal ion release,1 the assessment of surface topography of wires manufactured from these alloys is clinically important in terms of both safety and quality of orthodontic treatments.
The surface roughness of orthodontic archwires has been evaluated previously.2,16,17 However, previous studies have only been carried out on popular brands of archwires. The prices of archwires made by renowned companies and those made by others differ considerably, with the latter being approximately 5 to 10 times less expensive than the former. This may prompt orthodontists to use more economical products. Therefore, it is of great importance to assess the surface roughness of newly introduced and more economical wires because this characteristic is an essential factor influencing the effectiveness of arch-guided tooth movement2,3,5-7 and also contributes to the biocompatibility and esthetics of orthodontic appliances.2-5,10 However, the results obtained for materials of certain brands may not necessarily be applicable to products of other brands,18 and there have been no studies that have compared new wires with the more expensive wires. Therefore, the aim of this study was to investigate the surface roughness of 2 common types of orthodontic wires (SS and NiTi) manufactured by 4 different companies.
This study was designed as an in vitro experimental study. The sample size was 35 specimens of 7 different wires. Under the assumption that all the wires made by the same manufacturer undergo similar finishing processes,19 we examined 4 types of NiTi archwires (1 each from American Orthodontics, Sheboygan, WI, USA; OrthoTechnology, Tampa, FL, USA; All-Star Orthodontics, Columbus, IN, USA; and Smart Technology, Beijing, China) and 3 types of SS wires (1 each from American Orthodontics, OrthoTechnology, and All-Star Orthodontics), which are in conventional use. The wires had cross-sections of 0.016 × 0.022 inches and were studied as received. The archwires were first ultrasonically cleaned at 60℃ for 15 minutes with an alkaline solution (RamyarShimi, Tehran, Iran) and rinsed with distilled water to remove any precipitates. Five specimens, of length 20 mm, were then prepared from a straight portion of each archwire by using wire cutters.
SEM was used at ×1,000 magnification to assess the micromorphological characteristics of the archwires. Each specimen was mounted on a holder and observed under a field-emission SEM apparatus (Philips XL 30; Philips, Eindhoven, The Netherlands). To render the surfaces electron-opaque, the wires were coated with a 15- to 20-nm layer of gold by using a sputter coater (Physical Vapor Deposition; BAL-TEC, Zurich, Switzerland). The surfaces of the specimens were bombarded with electrons, and the intensity of the reflected electrons on each pixel were analyzed to obtain the SEM images. The surface characteristics were determined on the basis of a visual evaluation of the surface irregularities.
This system also was equipped with an energy-dispersive X-ray spectrophotometer (EDS) to analyze the chemical composition of the wire. The EDS received and analyzed the X-ray energy spectrum dispersed from the surface to distinguish the composition of the wire materials.
Surface profilometry was performed using a contact stylus profilometer (DEKTAK-3 version 2.13; Überlingen, Germany) to analyze the surface roughness of the wires. The profilometer was equipped with a metal vertically movable tip, which was sensitive to vertical movements at an accuracy of ± 0.01 Angstroms, and accurately probed and recorded the surface profile on five 3-mm-long sections of each specimen at medium speed (15 s). The irregular vertical movements of the tips were plotted against the profile of the surface explored. The distance examined at each scan was 3 mm. Three profilometric scans were performed at different parts of each wire. The equipment automatically determined the profilometric mean roughness from the surface profile.
Descriptive statistics were calculated. Since data distribution was not normal, the means and standard deviations were compared using the Kruskal-Wallis and Mann-Whitney U tests of the SPSS statistical package (version 16; SPSS Inc., Chicago, IL, USA). The level of significance was set at 0.05 for the Kruskal-Wallis test and adjusted using Bonferroni's method for pairwise comparisons.
The average Ni/Ti ratio in the NiTi wires was 1.415 ± 0.098, and the average ratio of Ni/Fe was 0.529 ± 0.162 (Table 1).
The surface topography of each NiTi archwire, as observed by SEM, is summarized in Figure 1. Each specimen had its own characteristic surface structure.
The scanning electron micrographs of the NiTi arch wire produced by All-Star Orthodontics showed more lines and grooves (parallel to the long axis of the archwire) than the samples of the other archwires (Figure 1C). Such irregularities were smallest in the archwire produced by Smart Technology. Pitting was another type of surface irregularity observed on all the samples; it was more visible on the archwire produced by Smart Technology and OrthoTechnology than those produced by the other manufacturers (Figure 2B and 2D).
The most common morphological patterns of the SS archwires observed on SEM analyses are summarized in Figure 2A-2C. As shown, the SS archwire produced by American Orthodontics showed more peaks and valleys than the other 2 samples. Further, it was clearly seen that the NiTi archwires have more defects and porosities than the SS archwires produced by the same manufacturers.
The average surface roughness values of NiTi and SS wires were 2,288.35 ± 2,174.33 A° and 2,189.47 ± 1,953.82 A°, respectively (Table 2, Figure 3), which did not significantly differ (p = 0.374) by the Mann-Whitney U test.
Analysis using the Kruskal-Wallis test showed a significant difference between the tested NiTi wires (p = 0.006). The NiTi wire manufactured by Smart Technology had the smoothest surface and shorter wavelength and lower amplitude than those manufactured by American Orthodontics, OrthoTechnology, and All-Star Orthodontics (Table 2, Figures 3 and 4).
The level of significance was adjusted to 0.008 for the following pairwise comparisons (Table 3). Statistically significant differences were noted between the surface roughness of NiTi wires produced by American Orthodontics and All-Star Orthodontics, and between those produced by All-Star Orthodontics, Smart Technology, and OrthoTechnology (Table 3).
The Kruskal-Wallis test showed a significant difference between the tested SS wires with respect to the degree of surface roughness (p = 0.024). The wire made by American Orthodontics had greater roughness, with distinctly higher amplitude with longer wavelength, than those made by OrthoTechnology and All-Star Orthodontics (Figure 5).
The measurements obtained for SS wires covered a wide range of variation in roughness. The mean and standard deviation of surface roughness of the SS wires produced by All-Star Orthodontics, OrthoTechnology, and American Orthodontics were 710 ± 210 A°, 1,831 ± 1,156 A°, and 4,018 ± 2,214 A°, respectively (Table 2, Figure 3).
The level of significance was modified to 0.016 for pairwise comparisons (Table 4). Statistically significant differences were observed only when comparing the roughness of the SS arch wires made by American Orthodontics and All-Star Orthodontics (Table 4). There were no statistical differences between the profilometric surface roughness of the SS wires produced by All-Star Orthodontics and OrthoTechnology (Table 4).
The findings of profilometry for all similar samples were consistent with the heterogeneity observed between them in the surface structures rendered by SEM.
The manufacturers of orthodontic wires generally do not disclose the exact composition and manufacturing process of the archwires.20 The speed of tooth movement depends on several factors, including the surface quality of the archwire.21
The surface roughness of orthodontic archwires may be measured using several methods, including laser spectroscopy, contact-surface profilometry, and atomic force microscopy.3,7 Bourauel et al.2 compared the surface roughness of different wires by using these 3 techniques.3,7 They stated that the results of these 3 methods generally correspond well.2 The wires as-received showed an inhomogeneous surface with different patterns of surface irregularities, which may be attributable to the manufacturing process. The surface structure depends on the complex manufacturing processes, the surface finish treatments, and the alloy used.2,3,22,23 A questionable aspect of this study is whether it is appropriate to generalize the findings obtained for only 5 samples of each wire to the entire wire. However, this method has also been adopted in other studies. Further, although some inhomogeneities were noted in the extent of surface roughness, the coefficients of variations were small in most cases. In addition, the significant statistical results obtained indicate that the number of the specimens was sufficient.
In this study, SEM showed differences in the patterns of irregularities on the NiTi wires produced by different manufacturers. However, the patterns observed on the 3 wires made in USA were similar to each other, with deep scratches parallel to the long axis of the wires. In contrast, the NiTi wire produced by Smart Technology lacked such clear horizontal grooves and had shallow dimples and pores or short grooves, which were strangely also noted in the NiTi product of American Orthodontics. A point of consideration in this regard is that the high magnification of SEM limited the investigation and interpretation of the surface topology of a smaller area of the wires.18 Moreover, the SEM images provide poorly reproducible subjective interpretations, which render comparisons with other interpretations difficult.18 Therefore, we additionally employed the objective technique of profilometry. The findings regarding the aforementioned NiTi wires obtained by profilometry confirmed the subjective interpretations; additionally, considerable variation was noted in the roughness of the surface of NiTi wires produced by All-Star Orthodontics and Smart Technology. The surfaces of the SS wires shared major similarities but varied in some details, more than did the NiTi wires. The 3 different patterns observed on the SS wires were longitudinal grooves, shallow porosities, and small elevations on the surfaces. The grooves and porosities observed in this study were similar to those observed in another study.3 The minor differences between the surfaces of the SS wires will allow the extraction of clear-cut conclusions only if the analysis includes several images at different magnifications. EDS showed that the elemental composition of the NiTi wires was similar to that of the SS wires. The nickel contents of the NiTi and SS wires were within the normal range.24
Bourauel et al.2 compared 11 NiTi wires and Proasoski et al.16 compared 9 NiTi wires with 1 SS wire and 1 beta titanium wire and both authors reported that the SS wire had the smoothest surface. Similarly, Shin et al.17 compared SS and NiTi wires and found that the SS wires were smoother. The SEM micrographs obtained in this study showed more porosities, scratches, and defects on the NiTi wires than on the SS wires, but the difference was not significant. Although our results, indicating the overall superior smoothness of the SS wires, were consistent with those of previous studies, the difference observed in this study was not statistically significant. This can be attributed to the decrease in the differences between the surface roughness of NiTi wires and SS wires because of the very high variation observed between the different samples of the same type of wire (the SS wires manufactured by All-Star Orthodontics and Smart Technology, and the NiTi wires of American Orthodontics and OrthoTechnology). This study showed that the NiTi wire of American Orthodontics was smoother than their SS wire. This result is contrary to the previous findings on this brand,2,16,17 and also to the results obtained for the products of other brands examined in this study, all of which showed that SS wires were smoother. This inconsistency may be attributed to the random sampling approach adopted in this study, whereby the selected parts may have been impaired during the manufacturing processes or delivery.
Surface roughness influences friction most directly when dry, unlubricated sliding occurs. Very rough surfaces can cause considerable friction because of the contact between and interlocking of peaks and valleys.16 Frictional force is considered a major factor in orthodontic mechanotherapy, and studies have clearly shown that each force employed for the retraction of a tooth must overcome frictional forces.25 Frictional losses in orthodontic force are reported to be the lowest when SS wires are employed, and the forces are said to increase in the following order; cobalt-chrome alloys, NiTi alloys, and beta titanium.2 Huang5 reported that although the chemical structure of the passive film on all tested NiTi wires was the same (containing mainly TiO2 with small amounts of NiO), the pitting corrosion resistance of NiTi wires from different manufacturers differs significantly. This suggested that inhomogeneous surfaces with different surface irregularities can be attributed to the manufacturing process.3 Therefore, the surface characteristics of the NiTi wires with deeper pits may be the result of their complex manufacturing processes and their proprietary surface treatments.26
Surface roughness is an important characteristic of archwires. It is associated with the esthetics of dental products, as well as their corrosion behavior and biocompatibility.2,7 The extreme variability in the surface roughness of orthodontic NiTi wires suggests that some manufacturers do not pay sufficient attention to the quality of their products.2 This study showed that the surface roughness of different wires varied considerably, irrespective of the reputation of their brands.
This study revealed that NiTi and SS wires did not differ significantly in terms of their surface roughness. Further, the NiTi wire made by All-Star Orthodontics and the SS wire made by American Orthodontics showed the greatest number porosities and defects. Our findings indicate that manufacturers need to pay more attention to reducing the surface roughness of their products in order to improve the safety and quality of orthodontic treatment.
Figures and Tables
![]() | Figure 1Scanning electron micrographs (× 1,000) of the nickel-titanium wires. A, American Orthodontics; B, OrthoTechnology; C, All-Star Orthodontics; D, Smart Technology. Length of the measuring bar = 0.02 mm. |
![]() | Figure 2Scanning electron micrographs of the stainless steel wires. A, American Orthodontics; B, OrthoTechnology; C, All-Star Orthodontics. Length of the measuring bar = 0.02 mm. |
![]() | Figure 3The mean surface roughness of the wires studied (in A°). All-Star, All-Star Orthodontics; Ortho, OrthoTechnology; AO, American Orthodontics; Smart, Smart Technology. |
![]() | Figure 4Examples of the results of profilometric scan of the nickel-titanium wires. A, Smart Technology; B, American Orthodontics; C, OrthoTechnology; D, All-Star Orthodontics. Data points = 600; R curser = 24 A° at 1,608.26 µm; M curser = 0 A° at 500.00 µm; vertical delta = -24 A°; horizontal delta = 1,108.36 A°. |
![]() | Figure 5Examples of the results of profilometric scan of the stainless steel wires. A, All-Star Orthodontics; B, OrthoTechnology; C, American Orthodontics. Data points = 600; R curser = 24 A° at 1,608.26 µm; M curser = 0 A° at 500.00 µm; vertical delta = -24 A°; horizontal delta = 1,108.36 A°. |
Table 1
Chemical composition of orthodontic archwires (weight per cent [Wt%]) measured by energy-dispersive X-ray analysis
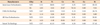
Table 2
The mean and standard deviation of the profilometric surface roughness of the NiTi and SS wires (n = 5, for all groups)
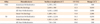
References
1. Faccioni F, Franceschetti P, Cerpelloni M, Fracasso ME. In vivo study on metal release from fixed orthodontic appliances and DNA damage in oral mucosa cells. Am J Orthod Dentofacial Orthop. 2003. 124:687–693.


2. Bourauel C, Fries T, Drescher D, Plietsch R. Surface roughness of orthodontic wires via atomic force microscopy, laser specular reflectance, and profilometry. Eur J Orthod. 1998. 20:79–92.


3. Daems J, Celis JP, Willems G. Morphological characterization of as-received and in vivo orthodontic stainless steel archwires. Eur J Orthod. 2009. 31:260–265.


4. Kusy RP, Whitley JQ, Mayhew MJ, Buckthal JE. Surface roughness of orthodontic archwires via laser spectroscopy. Angle Orthod. 1988. 58:33–45.
5. Huang HH. Variation in corrosion resistance of nickel-titanium wires from different manufacturers. Angle Orthod. 2005. 75:661–665.
6. Huang HH. Variation in surface topography of different NiTi orthodontic archwires in various commercial fluoride-containing environments. Dent Mater. 2007. 23:24–33.


7. Elayyan F, Silikas N, Bearn D. Ex vivo surface and mechanical properties of coated orthodontic archwires. Eur J Orthod. 2008. 30:661–667.


8. Rapiejko C, Fouvry S, Grosgogeat B, Wendler B. A representative ex-situ fretting wear investigation of orthodontic arch-wire/bracket contacts. Wear. 2009. 266:850–858.


9. Baccetti T, Franchi L, Camporesi M, Defraia E, Barbato E. Forces produced by different nonconventional bracket or ligature systems during alignment of apically displaced teeth. Angle Orthod. 2009. 79:533–539.


10. Widu F, Drescher D, Junker R, Bourauel C. Corrosion and biocompatibility of orthodontic wires. J Mater Sci Mater Med. 1999. 10:275–281.
11. Oshida Y, Sachdeva RC, Miyazaki S. Microanalytical characterization and surface modification of TiNi orthodontic archwires. Biomed Mater Eng. 1992. 2:51–69.


12. Amini F, Borzabadi Farahani A, Jafari A, Rabbani M. In vivo study of metal content of oral mucosa cells in patients with and without fixed orthodontic appliances. Orthod Craniofac Res. 2008. 11:51–56.


13. Amini F, Jafari A, Amini P, Sepasi S. Metal ion release from fixed orthodontic appliances--an in vivo study. Eur J Orthod. 2012. 34:126–130.


14. Bishara SE. Oral lesions caused by an orthodontic retainer: a case report. Am J Orthod Dentofacial Orthop. 1995. 108:115–117.


15. Staffolani N, Damiani F, Lilli C, Guerra M, Staffolani NJ, Belcastro S, et al. Ion release from orthodontic appliances. J Dent. 1999. 27:449–454.


16. Prososki RR, Bagby MD, Erickson LC. Static frictional force and surface roughness of nickel-titanium arch wires. Am J Orthod Dentofacial Orthop. 1991. 100:341–348.


17. Shin JS, Oh KT, Hwang CJ. In vitro surface corrosion of stainless steel and NiTi orthodontic appliances. Aust Orthod J. 2003. 19:13–18.
18. Khosravanifard B, Nemati-Anaraki S, Nili S, Rakhshan V. Assessing the effects of three resin removal methods and bracket sandblasting on shear bond strength of metallic orthodontic brackets and enamel surface. Orthod Waves. 2011. 70:27–38.


19. Kusy RP, Whitley JQ. Effects of surface roughness on the coefficients of friction in model orthodontic systems. J Biomech. 1990. 23:913–925.


20. Verstrynge A, Van Humbeeck J, Willems G. In-vitro evaluation of the material characteristics of stainless steel and beta-titanium orthodontic wires. Am J Orthod Dentofacial Orthop. 2006. 130:460–470.


21. Mohlin B, Müller H, Odman J, Thilander B. Examination of Chinese NiTi wire by a combined clinical and laboratory approach. Eur J Orthod. 1991. 13:386–391.


22. Neumann P, Bourauel C, Jäger A. Corrosion and permanent fracture resistance of coated and conventional orthodontic wires. J Mater Sci Mater Med. 2002. 13:141–147.
23. Pernier C, Grosgogeat B, Ponsonnet L, Benay G, Lissac M. Influence of autoclave sterilization on the surface parameters and mechanical properties of six orthodontic wires. Eur J Orthod. 2005. 27:72–81.


24. Brantley WA. Brantley WA, Eliades T, editors. Orthodontic wires. Orthodontic Materials: Scientific and Clinical Aspects. 2001. Stuttgart-New York: Thieme;77–105.
25. Kapila S, Sachdeva R. Mechanical properties and clinical applications of orthodontic wires. Am J Orthod Dentofacial Orthop. 1989. 96:100–109.


26. Jackson CM, Wagner HJ, Wasilewski RJ. NASA No SP 5110. 55-nitinol-the alloy with a memory--its physical metallurgy, properties and applications. 1972. Washington D.C.: