Abstract
PURPOSE
Vinyl polyether silicone (VPES) has a different composition from other elastomeric impression materials as it combines vinyl polysiloxane (VPS) and polyether (PE). Therefore, it is important to study its properties and behavior under different test conditions. This study investigated the dimensional stability of 5 VPES consistencies when stored for up to 2 weeks, with and without using a standard disinfection procedure.
MATERIALS AND METHODS
40 discs of each VPES consistency (total 200) were made using a stainless steel die and ring as described by ANSI /ADA specification No. 19. 20 discs of each material were immersed in a 2.5% buffered glutaraldehyde solution for 30 minutes. Dimensional stability measurements were calculated immediately after fabrication and repeated on the same discs after 7 and 14 days of storage. The data was analyzed using two-way ANOVA with a significance level set at α = 0.05.
RESULTS
The discs mean contraction was below 0.5% at all test times ranging from 0.200 ± 0.014 to 0.325 ± 0.007. Repeated measures ANOVA showed a statistically significant difference after 2-week storage between the disinfected and non-disinfected groups (P < .001). Although there was no statistically significant difference between the materials at the time of fabrication, the contraction of the materials increased with storage for 1 and 2 weeks.
Elastomeric impression materials undergo contraction upon polymerization due to cross-linking and rearrangement of bonds in polymer chains. Addition silicone and polyether impression materials undergo small dimensional changes of -0.15% and -0.20%, respectively, with half of the 24 hour contraction occurring within the first hour after setting.1
Several studies investigated the accuracy and dimensional stability of vinyl polysiloxane (VPS) and polyether (PE) impression materials under different test conditions such as the effect of prolonged storage, different levels of humidity and storage temperature on both impression material.2345 The main issues with polyether impression materials are water absoption and volatile substance release that can affect its dimensional stability, a problem which VPS does not experience due to the lack of polymerization byproducts.
On the other hand, and since it is not common for manufacturers to specify a certain disinfectant or disinfection protocol for impressions in order to control cross-contamination, several studies investigated different types of disinfectants and application methods on impression materials. Among the commonly used disinfectants, there have reports on the use of glutaraldehyde solutions. These studies showed that spray and immersion treatment of impressions using 0.5%, 2%, and 3.5% glutaraldehyde solutions for time ranging from 10 - 60 minutes did not cause any adverse effects on the accuracy or dimensional stability of PE and VPS impression material.67891011121314151617 Prolonged immersion of VPS impression materials overnight in 2% acid glutaraldehyde solution however resulted in adverse effects on the accuracy of the material.18 On the other hand, considering long-term storage of impression materials after 10-minute or 1-hour treatment with several disinfectants, a study showed that a 2-week storage of disinfected elastomers did not adversely affect the accuracy nor dimensional stability of the VPS and PE studied.19
A newer type of elastomer named EXA'lence (GC America Alsip, IL, USA) is available as a vinyl polyether silicone impression material (VPES). The manufacturer data sheet shows that it consists of a combination of two different elastomers. The major component of this material combines vinyldimethylpolysiloxane (10% to 50%), methylhydrogen dimethylpolysiloxane (3% to 10%), and silicone dioxide (30% to 65%), as well as the smaller portion of 5% - 20% PE to enhance hydrophilicity in the presence of fluids. Although studies have recommended to pour polyether impressions within an hour or up to 24 hours,202122 EXA'lence manufacturer claims that this PE-containing material has an outstanding dimensional stability even when the impression is not poured for up to 2 weeks. Two previous studies investigated the accuracy and dimensional stability of two EXA'lence consistencies, the medium body and the heavy body fast set. The two materials demonstrated excellent dimensional stability in vitro after undergoing disinfection and prolonged storage. The first study investigated EXA'lence 370 monophase regular set by making indirect measurements on casts poured from VPES impressions23 and the second one studied the heavy body fast set by making direct measurements on impression discs.24 Despite the different methods in testing the dimensional stability in these two studies, both materials demonstrated minimal dimensional changes after exposure to disinfection and prolonged storage.
In a continuing effort to improve understanding on the accuracy and dimensional stability of the different consistencies of VPES, this study investigated the effect of disinfection and storage on five EXA'lence impression materials that had different consistencies and setting time. The null hypothesis was that there would be no significant difference in the dimensional change of disinfected and non-disinfected discs of EXA'lence after prolonged storage in comparison to the control.
The 5 EXA'lence impression materials used in this study are described in Table 1. Direct linear measurements were made on impression discs (Fig. 1A) made on a metal die (Fig. 1B) that was used as the control for measurement comparisons. A total of 200 impression discs were made so that 40 discs were obtained for each consistency, of which 20 discs were randomly assigned for immersion disinfection treatment and the other 20 served as control.
The impression discs were fabricated according to ANSI/ADA specification no. 19 protocol25 using a stainless steel die and ring (Sabri Dental Enterprises, Inc., Downers Grove, IL, USA) (Fig. 1B) as described previously in detail.24 The use of the metal die and ring was first described in detail by Owen26 as laid down by International Standard ISO 1563-1978(E) for alginate impression material. The use of the die and ring allows the fabrication of identical impression discs that can be reproduced by other researchers to make precise comparison of the different materials once the specification protocol is properly followed. The resulting discs had 3 parallel lines that duplicate the three engraved lines A, B, and C on the metal die (Fig. 1). Line C which is 75 µm wide, was selected for making the measurements as it was shown by Owen that most materials failed to record the finer lines which measured 20 µ and 50 µ.
For the disinfection procedure, 20 discs of each impression material were immersed in a 2.5% buffered glutaraldehyde solution (Metricide 28; Metricide Research, Orange, CA, USA) at room temperature for 30 minutes, as recommended by the manufacturer, and then rinsed under running water for 15 seconds.
To assess dimensional stability, Line C on the discs (Fig. 1C) was measured between D1 and D2 immediately following fabrication. The discs were then stored in ambient laboratory conditions on a glass slab dusted with talcum. The measurements were repeated on the discs at 7 and 14 days.
The measurements were made on a milling machine with an X and Y table that has a digital readout with an encoder resolution of 5 µ. Each sample was placed onto a custom milled jig and aligned using a toolmaker microscope with a 30X magnification. The precise alignment allowed easy identification of the lines inscribed on the disc surface. The percentage of dimensional change was calculated as:
where L1 is the length of line C as measured on the metal die (25.070 mm) and L2 is the length of line C as measured on the discs. Once normal distribution of data was suggested, a repeated measures ANOVA was performed and P values < .05 were deemed to be statistically significant. Values are indicated as mean ± SE (standard error of mean) and reported in Table 2.
The length of line C between lines D1 and D2 as measured on the metal die (Fig. 1B) was 25.070 mm (L1). The dimensional changes among the evaluated discs at the three test times (immediate, after 7, and after 14 days) with and without disinfection are reported in Table 2 and illustrated in Fig. 2. Line C in all impression material discs (L2) was shorter than that on the control metal die, indicating contraction of all the materials at all times. The contraction of the discs was small with the mean percent values ranging from only 0.200 ± 0.014 to 0.325 ± 0.007, and a tendency for continuous contraction as time went by.
Considering the effect of disinfection on the evaluated materials, Fig. 2 shows the materials' contraction immediately, after one week, and after two weeks. For the immediate measurements, the percent value of contractions ranged from 0.200 ± 0.014 for the disinfected extra light regular set material (D ELR) to 0.253 ± 0.008 for the disinfected light body regular set one (D LR). There was no evidence of mean contraction differences between the disinfected and non-disinfected discs when measurements were made immediately after fabrication. The P value for the mean difference between the disinfected and non-disinfected samples of each set material was greater than 0.20.
After one week (Table 3 and Fig. 2), there was a statically significant difference between the disinfected and non-disinfected discs for the extra light body regular set (ELR) material only (P = .001). This difference may not be clinically significant. At 2 weeks (Table 4 and Fig. 2), there was a significant statistical mean difference between disinfected and non-disinfected extra light body fast set (ELF) (P < .001) and light body fast set (LF) (P < .001). There was also a weak evidence of statistically significant difference between the disinfected and non-disinfected extra light body regular set (ELR) (P = .057).
It is interesting to note that the disinfected and non-disinfected heavy rigid regular materials underwent the least increase in contraction from immediate to 2 weeks, where the percentage contraction values remained almost the same throughout the test period. This behavior is different from the light and extra light consistencies in this study, but is identical to the disinfected heavy body fast set VPES tested in a previous study.24
For the effect of storage time on the stability of the impression discs and considering all materials at the three test intervals, pairwise comparisons of the grouped five materials indicating that there was no statistically significant difference between the disinfected and non-disinfected materials at 0 or one week test times. However, there was a statistically significant difference after two weeks between the two groups (P < .001). Figure 3 shows that there was no difference in contraction right after fabrication of the discs, but there is a convincing tendency for a continuous contraction of both groups with time.
The null hypothesis was that there would be no significant difference in the dimensional change of disinfected and non-disinfected discs of VPES after prolonged storage in comparison to the control. The findings of this study reject this hypothesis as there was a statistically significant difference after two weeks of storage between the disinfected and the non-disinfected groups (P < .001).
As EXA'lence has a different composition from other elastomeric impression materials, it would be important to study its behavior under different test conditions. This study investigated the linear dimensional changes of 5 EXA'lence consistencies as a function of time using a well-established technique.3456912131517192324 As recommended by specification no.19 for elastomeric impression materials,25 a stainless steel die and ring was used to make the impression discs in order to measure dimensional changes. This technique allows for the identical reproduction of study conditions so that other investigators can make identical comparisons to other materials using the same test conditions or similar ones.
The mean contraction value of the polymerized materials was below 0.5% at all test times and conditions. The highest mean percent contraction was 0.325 ± 0.007 for the non-disinfected light body fast set measured at two weeks. These results comply with the recommendation of ANSI/ADA specification no.19 requirements for elastomeric impression materials. They are also consistent with the finding of two previous studies conducted on the dimensional stability of EXA'lence.2324 In the first study, identical conditions were employed to test the heavy body fast set EXA'lence where the average contraction for the disinfected group ranged from 0.190 ± 0.017 right after fabrication to 0.225 ± 0.015 at two weeks.24 In the second study, a different method was employed to test the medium body EXA'lence by making measurements indirectly on casts poured into a dental arch impression.23 The use of these two different methods may explain some differences in the results. Making 2D measurements directly on discs resulted in consistent readings with low standard deviations,24 which differed from measurements made indirectly on casts where variables such as dental stone, custom trays, and tray adhesive impacted the results leading to higher standard deviations. 23
Elastomeric materials contract upon setting mostly due to crosslinking and rearrangement of bonds within the polymer chains.1 Except for the heavy rigid material in this study, the evident continuous contraction of VPES could be the result of continuous polymerization and continuous evaporation of volatile substances from the polymerized elastomer leading to smaller measurements as shown in other studies.219 With continuous contraction, it is hard to assume how such material will behave when stored beyond two weeks, making it safe to pour the impression within this comfortable time limit. For each material tested, the amount of contraction increased very slightly with time which was shown to be the case in the previous study.19
Regarding the effects of disinfectants, several studies investigated the effect of glutaraldehyde on the dimensional accuracy of VPS and PE using different strengths and immersion intervals.6789101112131415161718 Although these studies found no adverse effect of using this disinfectant, longer immersion time was found to adversely affect the accuracy of the tested materials.18 Immersion of VPES in Glutaraldehyde for 30 minutes in this study did not affect its dimensional stability. Lepe et al.27 showed that while both VPS and PE exhibited some degree of imbibition when immersed in glutaraldehyde, PE lost 0.4% mass in air indicating loss of a volatile component. Lepe et al.14 also showed that when both PE and VPS exhibited some degree of imbibition during disinfection, the more wettable PE had a higher water imbibition than VPS but lost more mass in air than VPS, which gained some. Kanehira et al.2 showed that although VPS was not affected by storage, PE absorbed water but released volatile substances during storage and should be poured within 24 hours, which could explain the continuous contraction observed for VPES. Furthermore, it has been reported that PE imbibes water when immersed in a disinfectant leading to a significant increase in dimensional change after 24 hours. However, dimensional change remained constant between 0 and 60 minutes.12 Therefore, to interpret the effect of storage time and the immersion in disinfectant, it can be presumed that imbibition of water from the disinfectant could have caused the disinfected samples to exhibit less contraction with time, while the continuous polymerization led to equally increased contraction of all samples with time. Therefore, the disinfected sample in this case exhibited less contraction than the non-disinfected ones. A VPS impression material behaved in the same manner24 as disinfected Imprint 3 Quick Step (3M ESPE Dental Products, St. Paul, MN, USA) polymerization contractions were 0.263 ± 0.027 immediately, 0.281 ± 0.018 at one week, and 0.274 ± 0.019 at two weeks. This, however, did not apply to the nondisinfected discs that recorded 0.260 ± 0.008, 0.404 ± 0.013, and 0.409 ± 0.0125, respectively. Furthermore, it can be also speculated that immersion in the disinfectant could have caused less loss of volatile substance from the PE portion of the material. However, the only way to confirm such assumptions is to subject the material to a longer immersion time in disinfectant and/or measure its dimensional change after a much longer period of storage than two weeks.
Although there were statistically significant differences at one and two weeks storage period, such differences are of minor clinical impact as they still fit under the acceptable contraction values set by ANSI/ADA standard.25
This study attempted to evaluate the effect of a 30-minute immersion in one disinfectant only and a storage time of 2 weeks on the dimensional stability of EXA'lence. Although the materials underwent minimal contractions, it was not tested after longer storage periods or longer immersion time in disinfectant. It would be beneficial to study the effect of longer storage on the dimensional stability of EXA'lence in addition to studying the effect of other types of disinfectants and longer immersion periods.
30-minute immersion disinfection of EXA'lence discs in 2.5% buffered glutaraldehyde did not adversely affect their dimensional stability. The five materials studied underwent minimal contraction when stored for up to 2 weeks, with contraction values within ANSI/ADA specification No.19 for elastomeric impression materials. Contraction behavior of the materials was not studied after longer storage periods. Therefore it would be better to pour the impression within 2 weeks until further research provides more data.
Figures and Tables
Fig. 1
(A) Representative impression material disc, (B) The metal die used for making the discs, (C) Diagram of the metal ring showing line C measurement between points D1 and D2.
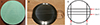
Table 1
VPES Materials used in the study
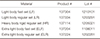
Table 2
Dimensional contraction % ΔL values of VPES (Mean ± SE) at 0, 7 and 14 day storage. These values are depicted in a graph in Fig. 2

Table 3
Pairwise comparisons of the materials showing the mean difference between disinfection and no disinfection, P value and 95% confidence interval of mean difference at one week storage
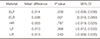
Material | Mean difference | P value | 95% CI |
---|---|---|---|
ELF | 0.014 | .208 | (−0.008, 0.036) |
ELR | 0.038 | .001 | (0.016, 0.060) |
HR | 0.003 | .787 | (−0.019, 0.025) |
LF | 0.010 | .368 | (−0.012, 0.032) |
LR | 0.013 | .243 | (−0.009, 0.035) |
Table 4
Pairwise comparisons of the materials showing the mean difference between disinfection and no disinfection, P value and 95% confidence interval of the mean difference at 2-week storage
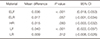
Material | Mean difference | P value | 95% CI |
---|---|---|---|
ELF | 0.036 | < .001 | (0.018, 0.053) |
ELR | 0.017 | .057 | (−0.001, 0.034) |
HR | 0.015 | .093 | (−0.003, 0.032) |
LF | 0.040 | < .001 | (0.022, 0.057) |
LR | 0.009 | .312 | (−0.008, 0.026) |
References
1. Sakaguchi RL, Powers JM. Craig's restorative dental materials. 13th ed. Philadelphia: Mosby Elsevier;2012. p. 293.
2. Kanehira M, Finger WJ, Endo T. Volatilization of components from and water absorption of polyether impressions. J Dent. 2006; 34:134–138.
3. Walker MP, Petrie CS, Haj-Ali R, Spencer P, Dumas C, Williams K. Moisture effect on polyether and polyvinylsiloxane dimensional accuracy and detail reproduction. J Prosthodont. 2005; 14:158–163.
4. Petrie CS, Walker MP, O'mahony AM, Spencer P. Dimensional accuracy and surface detail reproduction of two hydrophilic vinyl polysiloxane impression materials tested under dry, moist, and wet conditions. J Prosthet Dent. 2003; 90:365–372.
5. Corso M, Abanomy A, Di Canzio J, Zurakowski D, Morgano SM. The effect of temperature changes on the dimensional stability of polyvinyl siloxane and polyether impression materials. J Prosthet Dent. 1998; 79:626–631.
6. Yilmaz H, Aydin C, Gul B, Yilmaz C, Semiz M. Effect of disinfection on the dimensional stability of polyether impression materials. J Prosthodont. 2007; 16:473–479.
7. Kern M, Rathmer RM, Strub JR. Three-dimensional investigation of the accuracy of impression materials after disinfection. J Prosthet Dent. 1993; 70:449–456.
8. Jagger DC, Vowles RW, McNally L, Davis F, O'Sullivan DJ. The effect of a range of disinfectants on the dimensional accuracy and stability of some impression materials. Eur J Prosthodont Restor Dent. 2007; 15:23–28.
9. Melilli D, Rallo A, Cassaro A, Pizzo G. The effect of immersion disinfection procedures on dimensional stability of two elastomeric impression materials. J Oral Sci. 2008; 50:441–446.
10. Wadhwani CP, Johnson GH, Lepe X, Raigrodski AJ. ccuracy of newly formulated fast-setting elastomeric impression materials. J Prosthet Dent. 2005; 93:530–539.
11. Adabo GL, Zanarotti E, Fonseca RG, Cruz CA. Effect of disinfectant agents on dimensional stability of elastomeric impression materials. J Prosthet Dent. 1999; 81:621–624.
12. Davis BA, Powers JM. Effect of immersion disinfection on properties of impression materials. J Prosthodont. 1994; 3:31–34.
13. Rios MP, Morgano SM, Stein RS, Rose L. Effects of chemical disinfectant solutions on the stability and accuracy of the dental impression complex. J Prosthet Dent. 1996; 76:356–362.
14. Lepe X, Johnson GH, Berg JC, Aw TC, Stroh GS. Wettability, imbibition, and mass change of disinfected low-viscosity impression materials. J Prosthet Dent. 2002; 88:268–276.
15. Langenwalter EM, Aquilino SA, Turner KA. The dimensional stability of elastomeric impression materials following disinfection. J Prosthet Dent. 1990; 63:270–276.
16. Matyas J, Dao N, Caputo AA, Lucatorto FM. Effects of disinfectants on dimensional accuracy of impression materials. J Prosthet Dent. 1990; 64:25–31.
17. Thouati A, Deveaux E, Iost A, Behin P. Dimensional stability of seven elastomeric impression materials immersed in disinfectants. J Prosthet Dent. 1996; 76:8–14.
18. Lepe X, Johnson GH. Accuracy of polyether and addition silicone after long-term immersion disinfection. J Prosthet Dent. 1997; 78:245–249.
19. Walker MP, Rondeau M, Petrie C, Tasca A, Williams K. Surface quality and long-term dimensional stability of current elastomeric impression materials after disinfection. J Prosthodont. 2007; 16:343–351.
20. Donovan TE, Chee WW. A review of contemporary impression materials and techniques. Dent Clin North Am. 2004; 48:445–470.
21. Lacy AM, Fukui H, Bellman T, Jendresen MD. Time-dependent accuracy of elastomer impression materials. Part II: Polyether, polysulfides, and polyvinylsiloxane. J Prosthet Dent. 1981; 45:329–333.
22. Thongthammachat S, Moore BK, Barco MT 2nd, Hovijitra S, Brown DT, Andres CJ. Dimensional accuracy of dental casts: influence of tray material, impression material, and time. J Prosthodont. 2002; 11:98–108.
23. Nassar U, Oko A, Adeeb S, El-Rich M, Flores-Mir C. An in vitro study on the dimensional stability of a vinyl polyether silicone impression material over a prolonged storage period. J Prosthet Dent. 2013; 109:172–178.
24. Nassar U, Chow AK. Surface detail reproduction and effect of disinfectant and long-term storage on the dimensional stability of a novel vinyl polyether silicone impression material. J Prosthodont. 2015; 24:494–498.
25. American Dental Association Specification no. 19 for Nonaqueous, Elastomeric Dental Impression Materials. J Am Dent Assoc. 1977; 94:733–741.
26. Owen CP. An investigation into the compatibility of some irreversible hydrocolloid impression materials and dental gypsum products. Part I. Capacity to record grooves on the international standard die. J Oral Rehabil. 1986; 13:93–103.
27. Lepe X, Johnson GH, Berg JC. Surface characteristics of polyether and addition silicone impression materials after long-term disinfection. J Prosthet Dent. 1995; 74:181–186.