Abstract
Purpose
The purpose of this study is to evaluate the displacement of artificial tooth of monolithic complete denture manufactured by milling and 3D printing method in which the denture base and the artificial teeth are simultaneously made.
Materials and methods
Twelve upper and lower complete dentures for each were made by milling and 3D printing method. Group Up and Group Lp are a group of upper and lower dentures made by printing, and Group Um and Group Lm are denture groups made by milling. Group Uc and Group Lc are is a group of finally designed upper and lower dentures respectively. Measurements were performed between both central incisors (AB, ab), both canines (CD, cd), both first molars (EF, ef), between an incisor and a first molar (AE, ae), and between incisor and lingual point (AG, ag) for each upper and lower denture.
Results
AG and ag value between printed dentures and original ones as well as between milled dentures and original ones showed a statistically significant difference (One-way ANO-VA, P<.05) in both lower and upper monolithic dentures. In the lower monolithic ones, ab, cd and ef value revealed a significant difference between Group Lp and Group Lm (One-way ANOVA, P<.05).
REFERENCES
1.Dubojska AM., White GE., Pasiek S. The importance of occlusal balance in the control of complete dentures. Quintessence Int. 1998. 29:389–94.
2.Wong DM., Cheng LY., Chow TW., Clark RK. Effect of processing method on the dimensional accuracy and water sorption of acrylic resin dentures. J Prosthet Dent. 1999. 81:300–4.


3.Teraoka F., Takahashi J. Controlled polymerization system for fabricating precise dentures. J Prosthet Dent. 2000. 83:514–20.


4.Peyton FA. History of resins in dentistry. Dent Clin North Am. 1975. 19:211–22.
5.Murray MD., Darvell BW. The evolution of the complete denture base. Theories of complete denture retention-a review. Part 1. Aust Dent J. 1993. 38:216–9.
6.Kimoto S., Kobayashi N., Kobayashi K., Kawara M. Effect of bench cooling on the dimensional accuracy of heat-cured acrylic denture base material. J Dent. 2005. 33:57–63.


7.Consani RL., Mesquita MF., Sobrinho LC., Sinhoreti MA. Dimensional accuracy of upper complete denture bases: the effect of metallic flask closure methods. Gerodontology. 2009. 26:58–64.


8.Skinner EW., Cooper EN. Physical properties of denture resins: part I: curing shrinkage and water sorption. J Am Dent Assoc. 1943. 30:1845–52.


9.Elahi JM., Abdullah MA. Effect of different polymerization techniques on dimensional stability of record bases. J Prosthet Dent. 1994. 71:150–3.


10.Negreiros WA., Consani RL., Mesquita MF., Sinhoreti MA., Faria IR. Effect of flask closure method and post-pressing time on the displacement of maxillary denture teeth. Open Dent J. 2009. 3:21–5.


11.Rizzatti-Barbosa CM., Machado C., Joia FA., dos Santos Sousa RL. A method to reduce tooth movement of complete dentures during microwave irradiation processing. J Prosthet Dent. 2005. 94:301–2.


12.Badel T., Panduric′ J., Kraljevic′ S., Dulcic′ N. Checking the occlusal relationships of complete dentures via a remount procedure. Int J Periodontics Restorative Dent. 2007. 27:181–92.
13.Bidra AS., Taylor TD., Agar JR. Computer-aided technology for fabricating complete dentures: systematic review of historical background, current status, and future perspectives. J Prosthet Dent. 2013. 109:361–6.


14.Goodacre CJ., Garbacea A., Naylor WP., Daher T., Marchack CB., Lowry J. CAD/CAM fabricated complete dentures: concepts and clinical methods of obtaining required morphological data. J Prosthet Dent. 2012. 107:34–46.


15.Infante L., Yilmaz B., McGlumphy E., Finger I. Fabricating complete dentures with CAD/CAM technology. J Prosthet Dent. 2014. 111:351–5.


16.Kattadiyil MT., Goodacre CJ., Baba NZ. CAD/CAM complete dentures: a review of two commercial fabrication systems. J Calif Dent Assoc. 2013. 41:407–16.
17.Kanazawa M., Inokoshi M., Minakuchi S., Ohbayashi N. Trial of a CAD/CAM system for fabricating complete dentures. Dent Mater J. 2011. 30:93–6.


18.Inokoshi M., Kanazawa M., Minakuchi S. Evaluation of a complete denture trial method applying rapid prototyping. Dent Mater J. 2012. 31:40–6.


19.Baba NZ., AlRumaih HS., Goodacre BJ., Goodacre CJ. Current techniques in CAD/CAM denture fabrication. Gen Dent. 2016. 64:23–8.
20.Wimmer T., Gallus K., Eichberger M., Stawarczyk B. Complete denture fabrication supported by CAD/CAM. J Prosthet Dent. 2016. 115:541–6.


21.Yamamoto S., Kanazawa M., Iwaki M., Jokanovic A., Minakuchi S. Effects of offset values for artificial teeth positions in CAD/CAM complete denture. Comput Biol Med. 2014. 52:1–7.


22.Yamamoto S., Kanazawa M., Hirayama D., Nakamura T., Arakida T., Minakuchi S. In vitro evaluation of basal shapes and offset values of artificial teeth for CAD/CAM complete dentures. Comput Biol Med. 2016. 68:84–9.


23.Sayed ME., Swaid SM., Porwal A. Effect of cast modification on linear dimensional change of acrylic tooth position following maxillary complete denture processing. J Prosthodont. 2016 Feb 16.


24.Shibayama R., Gennari Filho H., Mazaro JV., Vedovatto E., Assunção WG. Effect of flasking and polymerization techniques on tooth movement in complete denture processing. J Prosthodont. 2009. 18:259–64.


25.Salloum AM. Effect of three investing materials on tooth movement during flasking procedure for complete denture construction. Saudi Dent J. 2016. 28:56–61.


26.Kishi M. Experimental studies on the relation between area and displacement of loading surfaces in connection with displaceability in the mucosa of edentulous alveolar ridge under pressure. Shikwa Gakuho. 1972. 72:17–45.
27.Park C., Kim MH., Hong SM., Go JS., Shin BS. A study on the comparison mechanical properties of 3D printing prototypes with laminating direction. J Korean Soc Manufactur Technol Eng. 2015. 24:334–41.


28.Objet Eden 260VS. Stratasys Ltd., Available at. http://www.strata-sys.com.
Fig. 1.
Measuring points designed on the image of upper denture. (A) 3 dimensional image of upper denture with seven measuring points (A - F), (B) measuring points of upper anterior region, (C) measuring ones of upper molars.
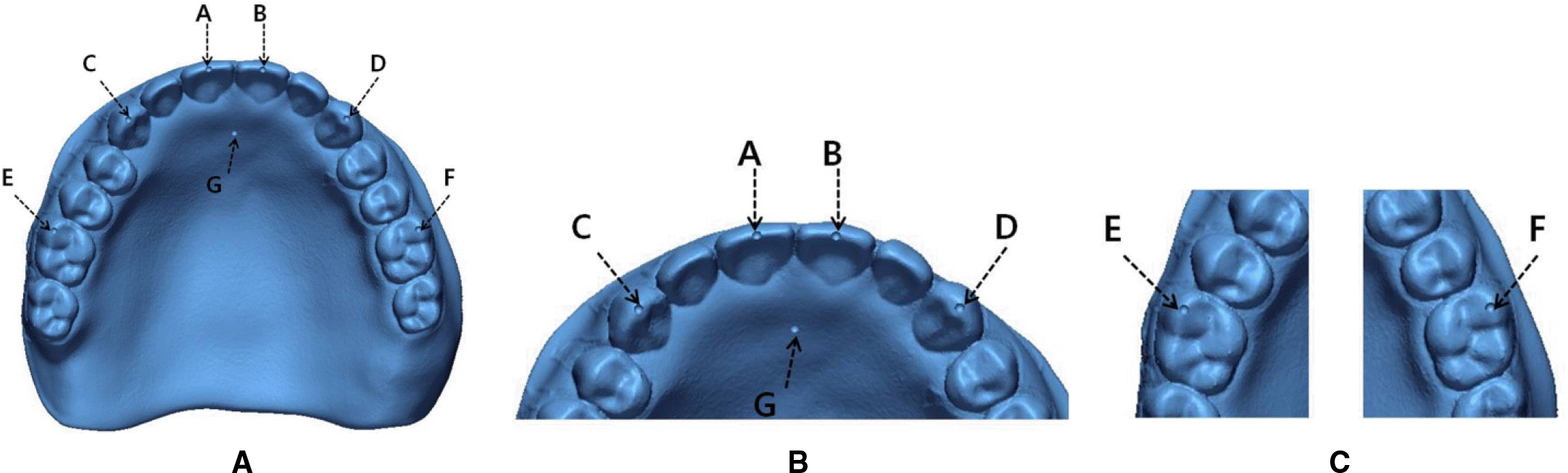
Fig. 2.
Measuring points designed on the image of lower denture. (A) 3 dimensional image of lower denture with seven measuring points (a - f), (B) measuring points of lower anterior region, (C) measuring ones of lower molars.
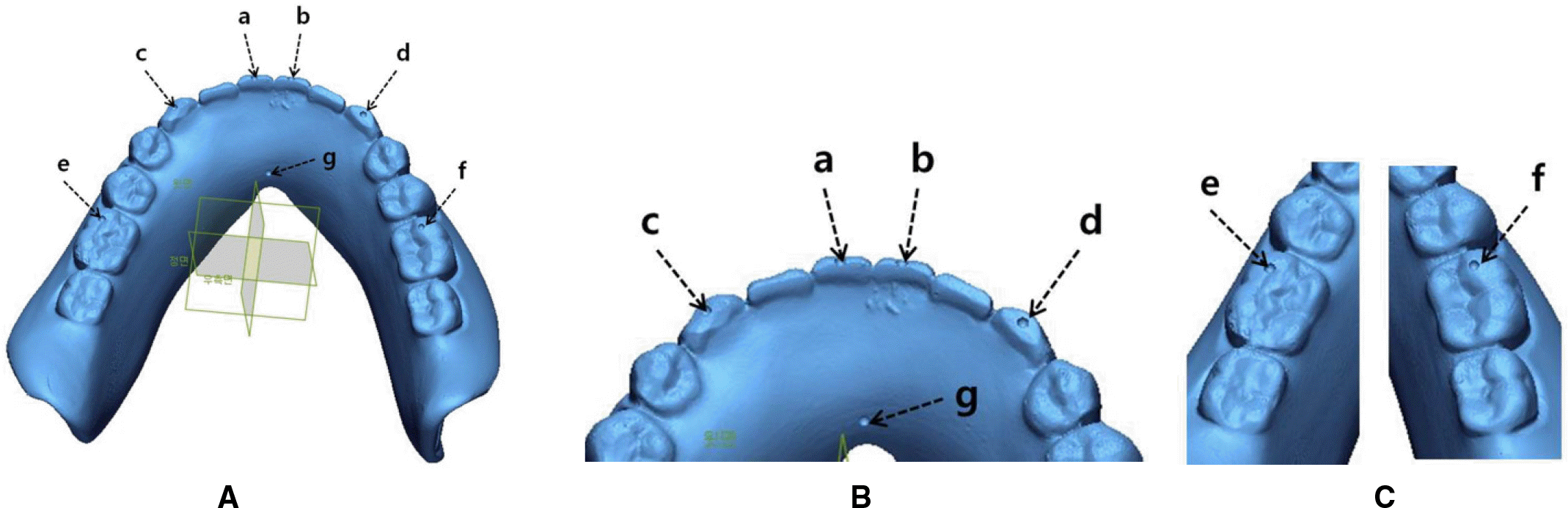
Fig. 3.
Monolithic complete denture made by 3D Printer and milling machine. (A, B) upper and lower one by 3D printer, (C, D) upper and lower one by milling machine.
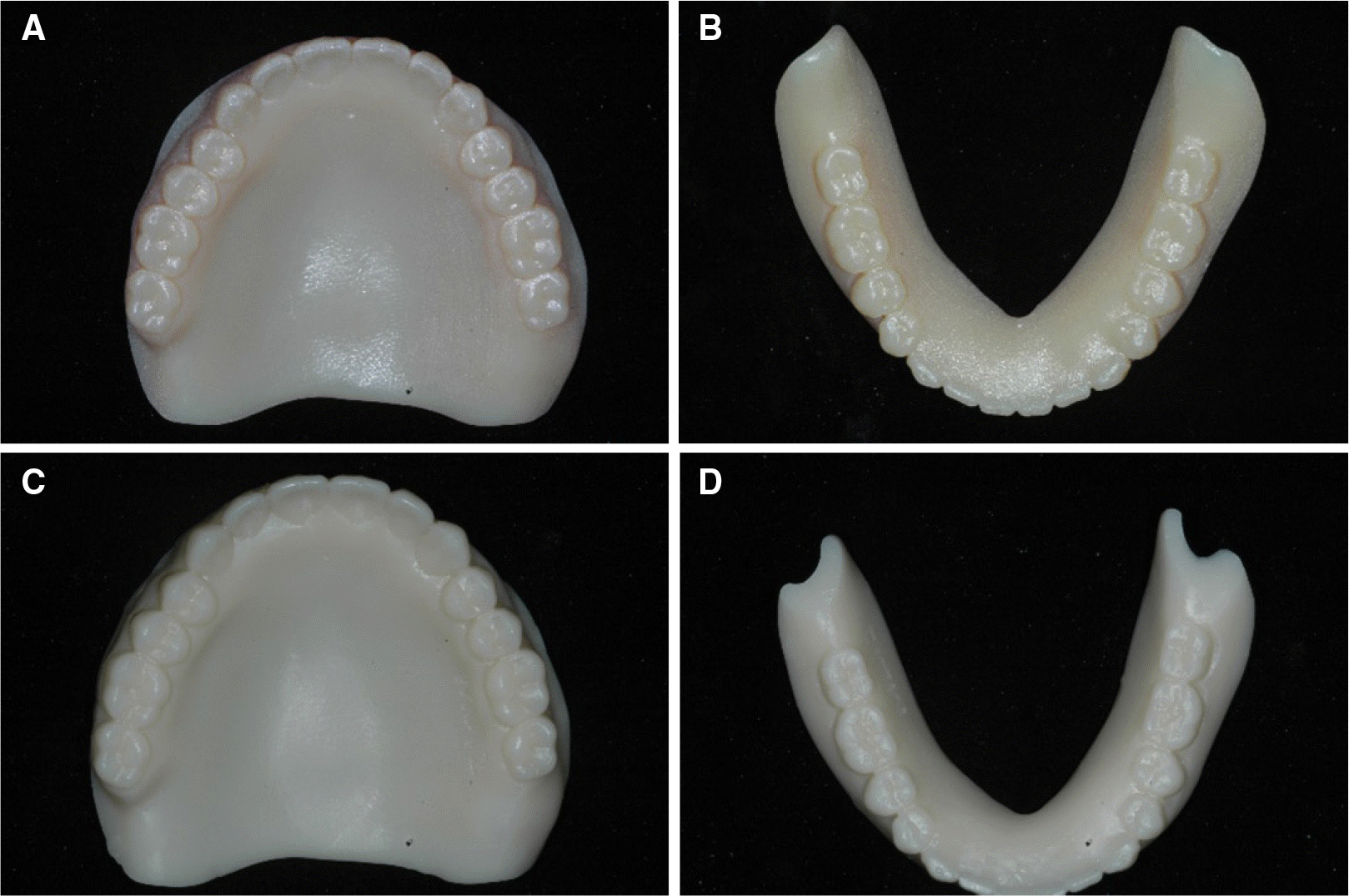
Table 1.
Mean value of distance between measuring points in upper denture (Unit: mm)
Table 2.
Mean value of dstance between lower points (Unit: mm)