Abstract
Purpose
The purpose of this study was to evaluate the level of electrochemical corrosion and surface roughness change for the cases of Ti abutment connected to restoration made of base metal alloys.
Materials and methods
It was hypothesized that Ni-Cr alloys in different compositions possess different corrosion resistances, and thus the specimens (13×13×1.5 mm) in this study were fabricated with 3 different types of metal alloys, commonly used for metal ceramic restorations. The electrochemical characteristics were evaluated with potentiostat (Parstat 2273A) and the level of surface roughness change was observed with surface roughness tester. Paired t-test was used to compare mean average surface roughness (Ra) changes of each specimen group.
Results
All specimens made of nickel-chromium based alloys, average surface roughness was increased significantly (P < .05). Among them, the Ni-Cr-Be alloy (0.016 ± 0.007 μ m) had the largest change of roughness followed by Ni-Cr (0.012 ± 0.003 μ m) and Ni-Cr-Ti (0.012 ± 0.002 μ m) alloy. There was no significant changes in surface roughness between each metal alloys after corrosion.
REFERENCES
1.Council on Dental Materials, Instruments, and Equipment. American Dental Association status report on the occurrence of galvanic corrosion in the mouth and its potential effects. J Am Dent Assoc. 1987. 115:783–7.
2.Geis-Gerstorfer J., Weber H., Sauer KH. In vitro substance loss due to galvanic corrosion in Ti implant/Ni-Cr supraconstruction systems. Int J Oral Maxillofac Implants. 1989. 4:119–23.
3.Goehlich V., Marek M. Corrosion behavior of Pd-Cu and Pd-Co alloys in synthetic saliva. Dent Mater. 1990. 6:103–10.


4.Schmalz G., Garhammer P. Biological interactions of dental cast alloys with oral tissues. Dent Mater. 2002. 18:396–406.


5.Wylie CM., Shelton RM., Fleming GJ., Davenport AJ. Corrosion of nickel-based dental casting alloys. Dent Mater. 2007. 23:714–23.


6.Gil FJ., Sa′nchez LA., Espl′as A., Planell JA. In vitro corrosion behaviour and metallic ion release of different prosthodontic alloys. Int Dent J. 1999. 49:361–7.


7.Venugopalan R., Lucas LC. Evaluation of restorative and implant alloys galvanically coupled to titanium. Dent Mater. 1998. 14:165–72.


8.Quirynen M., Bollen CM. The influence of surface roughness and surface-free energy on supra- and subgingival plaque formation in man. A review of the literature. J Clin Periodontol. 1995. 22:1–14.
9.Bollen CM., Lambrechts P., Quirynen M. Comparison of surface roughness of oral hard materials to the threshold surface roughness for bacterial plaque retention: a review of the literature. Dent Mater. 1997. 13:258–69.
10.Bollen CM., Papaioanno W., Van Eldere J., Schepers E., Quirynen M., van Steenberghe D. The influence of abutment surface roughness on plaque accumulation and peri-implant mucositis. Clin Oral Implants Res. 1996. 7:201–11.


11.ISO 10271 Standard. Dental metallic materials-corrosion test methods. 1st ed.Switzerland: ISO Geneva;2001.
12.Kay KS., Chung CH., Kang DW., Kim BO., Hwang HG., Ko YM. A study on the galvanic corrosion of titanium using the immersion and electrochemical method. J Korean Acad Prosthodont. 1995. 33:584–609.
13.Oh KT., Kim KN. Electrochemical properties of suprastructures galvanically coupled to a titanium implant. J Biomed Mater Res B Appl Biomater. 2004. 70:318–31.


14.Lucas LC., Lemons JE. Biodegradation of restorative metallic systems. Adv Dent Res. 1992. 6:32–7.


15.Choi BC., Kim CW. Corrosion of porcelain-fused-to-metal alloys. Dent Mater J SNU. 1992. 2:155–189.
16.Korean council for the faculty of dental materials. Dental materials. 4th ed.Seoul: Koonja publishing Inc.;2006. p. 335–6.
Fig. 4.
Light micrographs of specimens (original magnification ×500). All specimen (white area - Nickel, black area - Chrome). A, B: NB group had large grain size and well defined boundary. C, D : Crystal of alloy was distributed uniformly. E, F: Group NT had similar crystal structure.
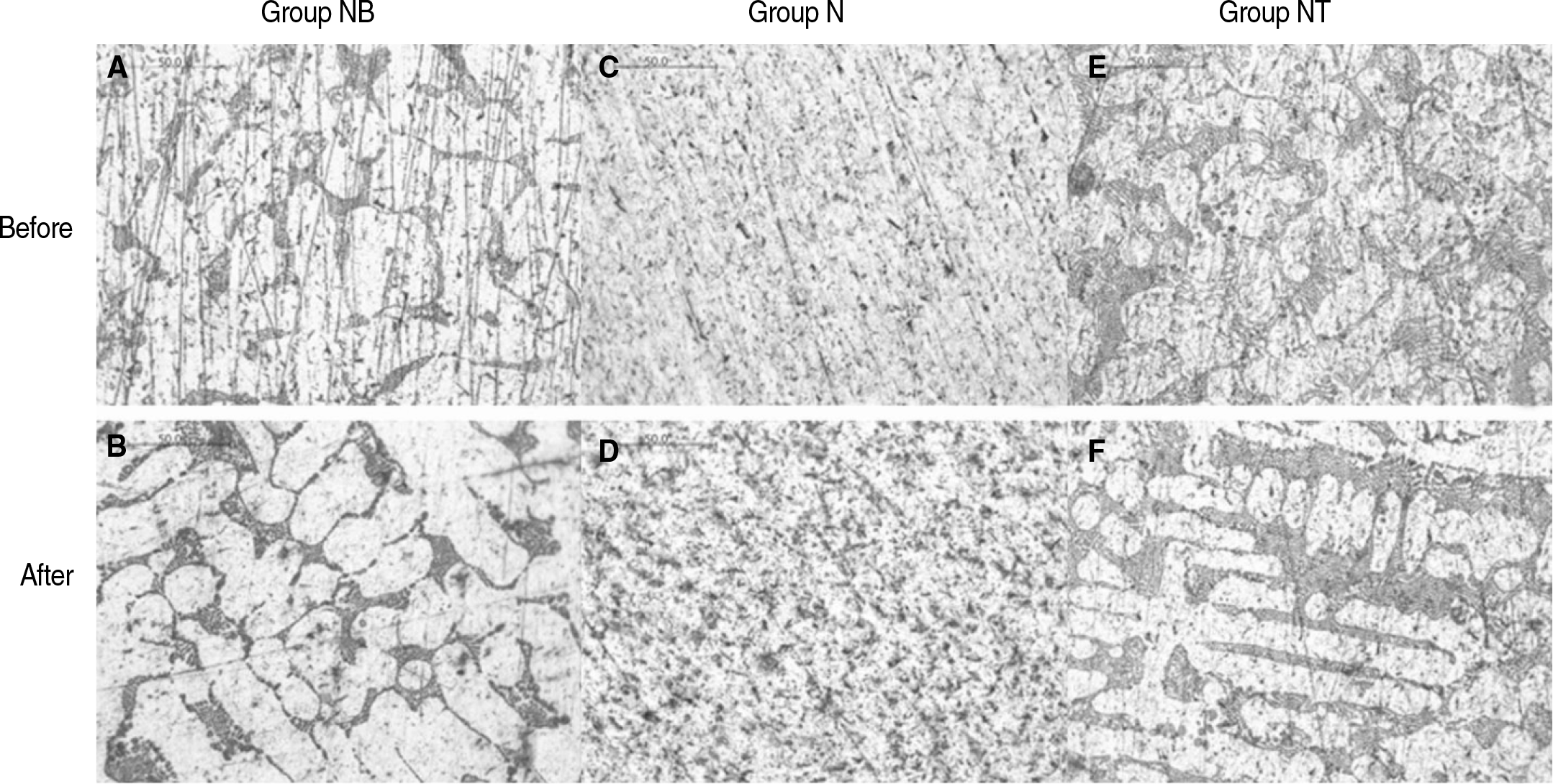
Fig. 5.
SEM micrographs of specimens (original magnification ×1,000). A, B: Group NB, C, D: Group N, E, F: Group NT.
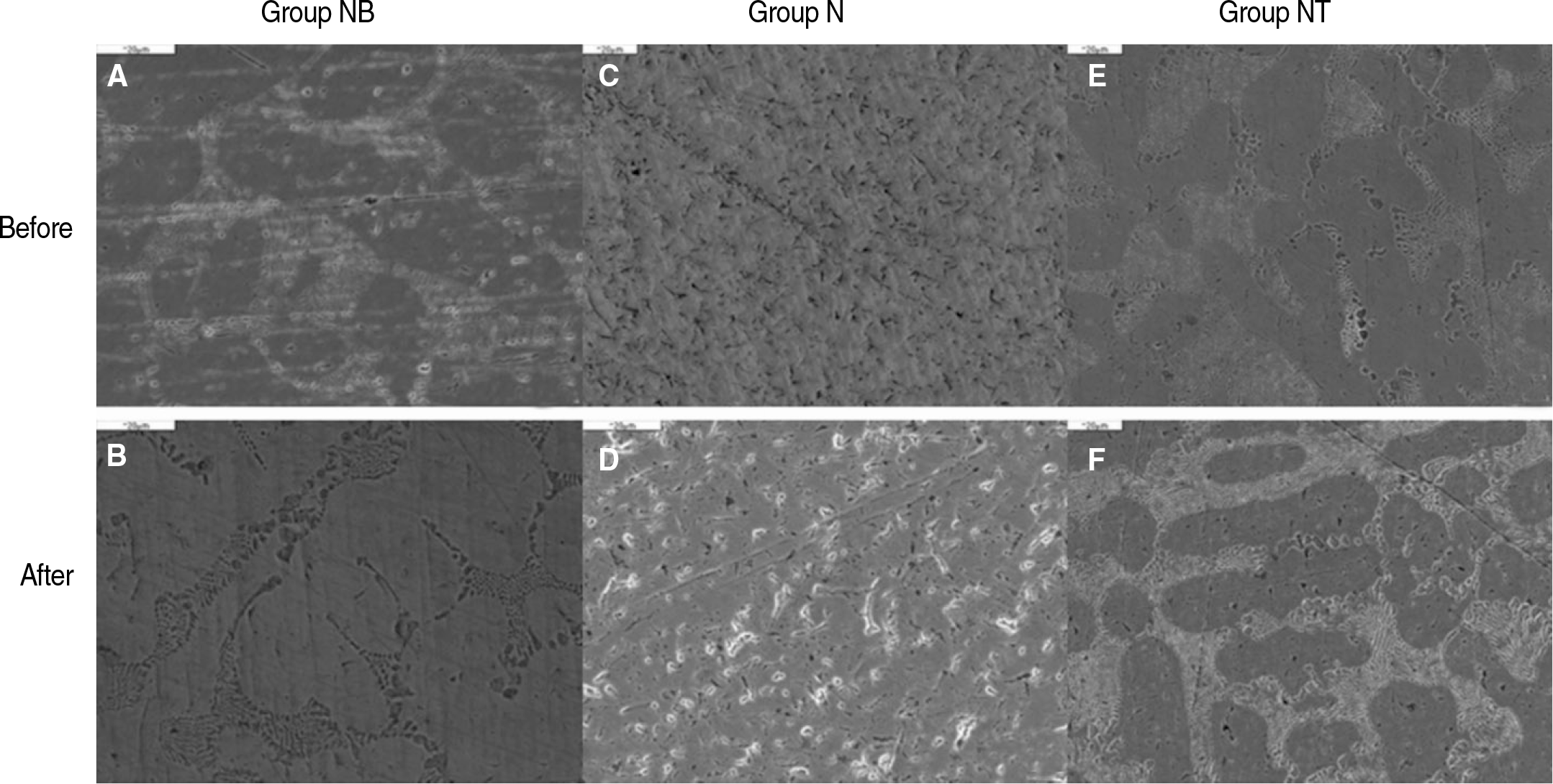
Table 1.
Materials used in this study
Table 2.
Constituents of Electrolyte
Constituent | Concentration (g/L) |
---|---|
DW | bal. |
Lactic acid | 10 |
NaCl | 5.85 |
Table 3.
Electrode and scanning conditions in this study
Table 4.
Chemical composition of Ni-Cr alloys by EDX analysis (%)
NB | N | NT | |
---|---|---|---|
Ni | 78.47 | 67.31 | 78.53 |
Cr | 14.04 | 22.60 | 13.09 |
Mo | 5.10 | 10.08 | 6.02 |
Al | 1.88 | - | 1.90 |
Fe | - | - | - |
Ti | - | - | 0.47 |
Table 5.
Value of corrosion potential (Ecorr) voltage (V (SCE)) of Ni-Cr
Group | Corrosion potential (Ecorr) |
---|---|
NB | -0.173 |
N | -0.296 |
NT | -0.199 |